Prefab performers: 16 of the top rating modular and prefabricated homes

If you still think prefab is code for ‘cookie cutter’ you’d be wrong. There has been a widespread architectural revolution when it comes to prefabricated construction; now, almost any design is possible. We look at the latest developments in Australia.
In this special feature, we speak with 16 companies offering what can be called ‘prefabricated’, ‘factory’ or ‘off-site’ construction services. We have selected those with a focus on the residential sector and which provide options for high building energy star ratings, renewable materials and cost-effective production.
We provide a summary below. For further details on each company’s offering including price per square metre, construction time to lockup, and details of the projects pictured, please read the full article in Sanctuary 42.
1. Modscape
Modular construction, steel frame
Since it was established over a decade ago, Modscape has seen its business shift from servicing remote and holiday locations with prefabricated modular homes, to delivering the majority of its projects to inner city sites. Modscape can provide structural modules only, through to a “one stop shop” that includes full internal fit-out, landscaping, solar + battery systems and waste water treatment, among other services. It has always used sustainable materials and now takes a ‘closed loop’ approach that has seen it move to using recyclable steel frames for 90 per cent of its projects.

2. Ecoliv Buildings
Modular construction, timber frame
Running for over 10 years, Ecoliv Buildings is based in the regional Victorian town of Wonthaggi, and delivers projects around Australia. Its approach is based squarely in sustainability. The company says each of its homes is resource-efficient and combines passive solar design, construction waste reduction and systems integration. Its process focuses on optimising operational performance using modular prefabricated construction. Solar electricity and hot water, efficient lighting and 10,000 litres of rainwater storage also come standard with Ecoliv homes to reduce environmental impact.

3. Prebuilt and Pleysier Perkins
Modular construction, steel frame
Starting out 15 years ago, Prebuilt is a veteran in the Australian modular and prefab industry. These days, while about 60 per cent of its work is in the commercial sector, Prebuilt completes about 18 residential projects each year around Australia, offering predesigned houses and custom designs, usually in partnership with architects Pleysier Perkins. “Custom designs are more and more in demand, especially in Sydney where there are often difficult sites and tight planning restrictions,” says Prebuilt’s Laura Batch. The company uses a modular system: engineered for the specific site and design requirements of the project, the modules consist of steel structural members with traditional timber frame infill. Insulation, cladding, utilities and the entire internal fit-out is also completed in their Kilsyth factory in Victoria.

4. Archiblox
Modular construction, timber frame
Archiblox opened shop in 2012 and already has the capacity to complete 40 to 60 modular housing projects per year, depending on the balance of bespoke and ‘smart’ designs on the books. “We encourage people to consider our smart designs because we can achieve greater efficiencies with cost and coordination of the build,” says Archiblox founder Bill McCorkell, who’s both an architect and builder. There are at least 11 Archiblox ‘smart designs’ to work from, and each modular building can be modified to suit the client and site; special care is taken with regard to orienting for passive solar design and to capture views without affecting thermal performance.

5. Arkit
Modular and panelised construction systems
Arkit designs and uses modular and panelised construction. The approach used is determined by which will achieve the best outcome, based on the site. The company uses similar materials regardless of the approach taken; timber frames, well-sealed double-glazed windows, Passivhaus certified ProClima building wrap, formaldehyde-free OSB and high-density insulation are features of each system. As much of the build as possible is prefabricated within the factory environment, with internal wall linings, footings and services connected on site.

6. Habitech Systems
Panelised construction system, using SIPs
Habitech Systems has developed its own sustainable building components based on an integrated wall and roof panel system. Founded in 2008 by architect Chris Barnett, the company offers full architectural design services, with a strong focus on thermal performance and healthy interiors. Using its own SIPs (structural insulated panels) which include an integrated cladding system, Habitech uses a growing network of local builders to deliver its projects. The science behind the building system aligns with the Passivhaus standard, and Habitech also works collaboratively with other architects. The majority of Habitech’s clients are in Australia’s southern states, but it has also partnered with builders in New Zealand to distribute its product and services there.

7. Carbonlite
Panelised construction system; supplies building envelopes to builders & homeowners
Panellite is a prefabricated timber wall, floor and roof system from Australian company Carbonlite. Carbonlite director Burkhard Hansen is a certified Passivhaus builder with international experience in prefabrication. He launched Panellite in 2015 to provide a flexible panelised system that can be used for any design to achieve the Passivhaus performance standard, and the company routinely provides blower door and pressure testing for completed projects. While Carbonlite can provide design and construction services, its primary business is supplying high-quality building shells for builders and homeowners.
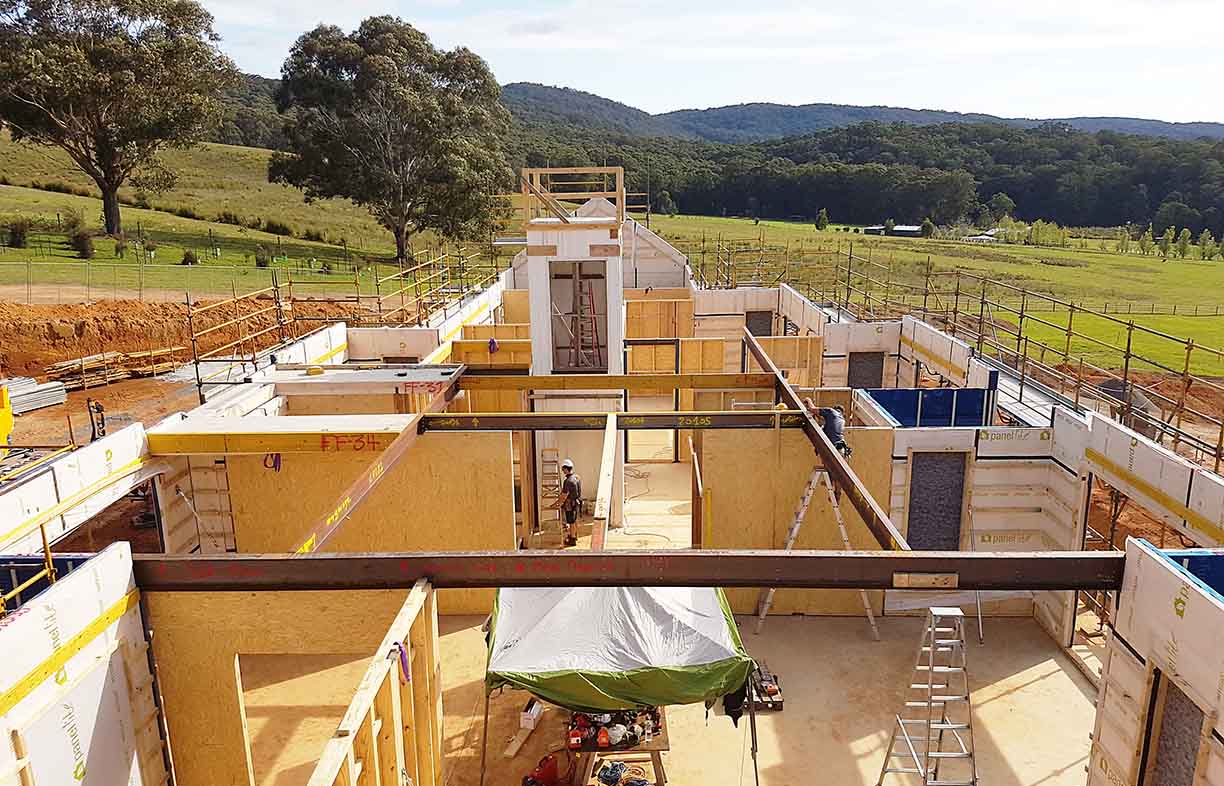
8. Makers of Architecture
Panelised construction system, deconstructable
Wellington-based Makers of Architecture and construction company Makers Fabrication work together and collaboratively with other designers, using digital technology and CNC (computer numerical control) capabilities to create custom designs efficiently. While Makers can work with a variety of construction systems, the Warrander Studio is a great example of the ‘CLT with cladding cassette’ system developed specifically to make the most of their design and fabrication technology. CNC-cut cross laminated timber (CLT) panels provide the structure and interior lining; prefabricated plywood cassettes containing insulation, service runs and external fibre cement sheet cladding are fitted to the exterior CLT panels using pre-routed slots. A timber ‘rain screen’ connects to the exterior of the cladding cassettes, providing the final skin.
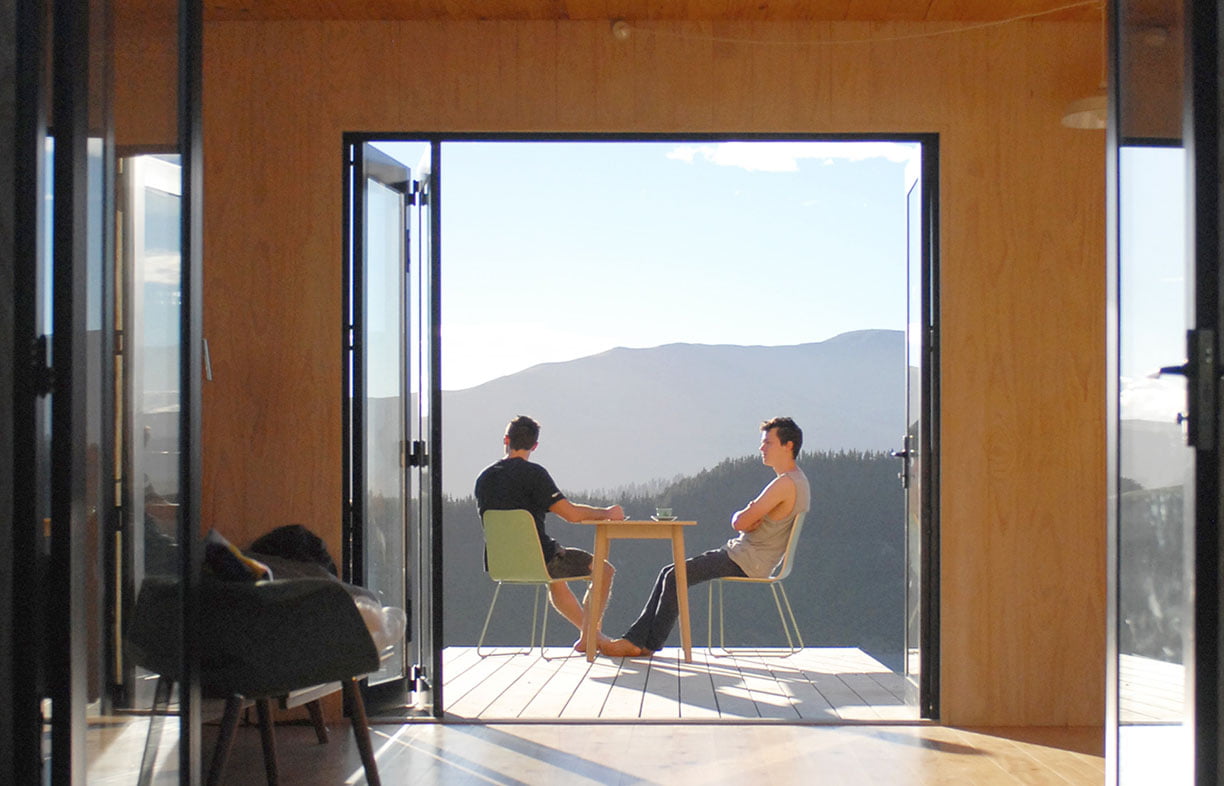
9. Ehabitat
Modular construction
Ehabitat has offices in Hobart and Melbourne and is a firm of five staff and a small factory. There are no off-the-shelf plans, with each building custom-designed to suit both client needs and the site. Passive solar design is embedded in the system, with low embodied energy materials chosen throughout. The prefab approach “allows quick construction, reducing on-site labour costs by up to 40 per cent,” says Ehabitat’s Giles Newstead. “Our modular system uses low-cost, off-the-shelf materials which can be used with no cutting. This means all internal and external cladding (including glass) just ‘plugs’ straight into the frame.” The system is deliberately space-efficient, and there are many clever built-in storage and space saving options included.

10. Ecoshelta
Modular and panelised construction systems, aluminium alloy
Ecoshelta runs a small architecture-oriented prefabricated modular building practice with workshops in Sydney and Hobart. It has made small, prefabricated buildings for over 30 years, and has experience using solid timber frames, manufactured timber elements, steel and now marine grade structural aluminium alloy. The company has a strong focus on technology, and uses a combination of natural and manufactured products, composite panel elements and 3D-printed materials. It also uses the proprietary ‘EcoCost’ environmental costing system to provide clients with a full life cycle assessment of the raw materials.
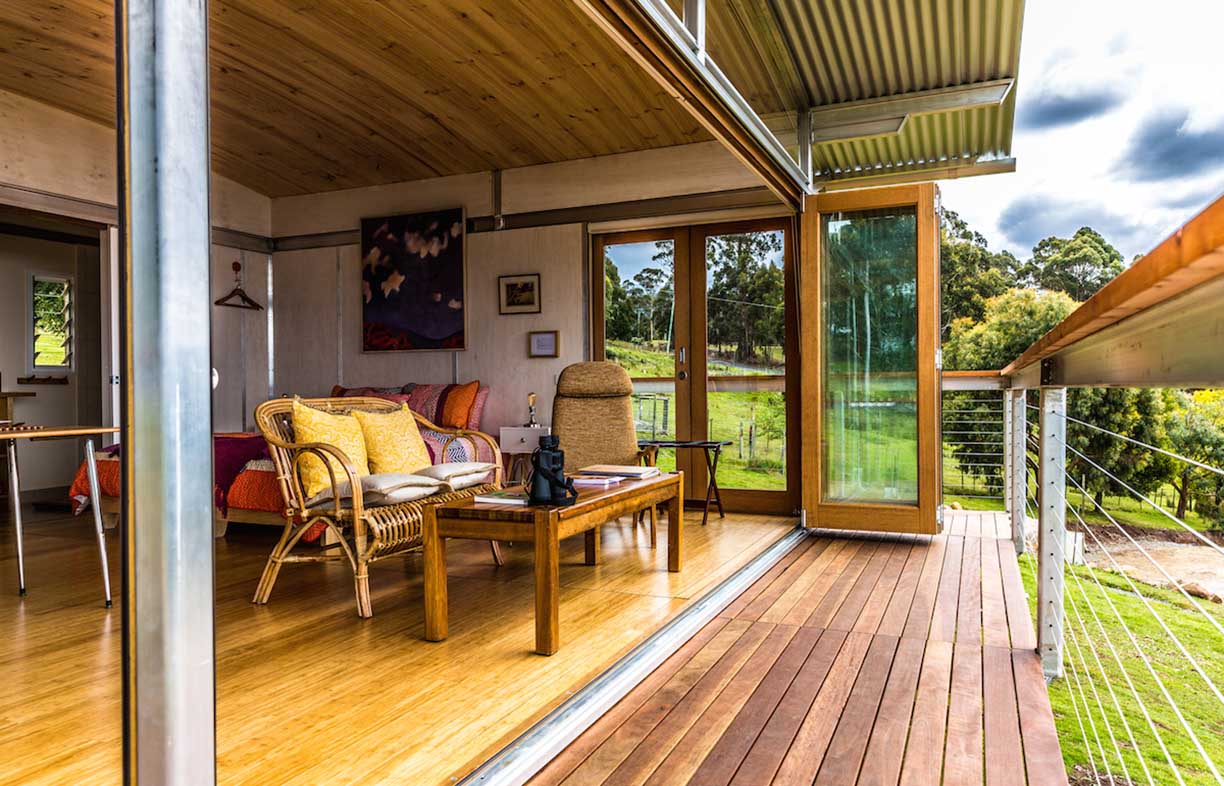
11. Impresa House
Panelised construction system, timber frame
Impresa House opened its Derrimut factory in Victoria in October 2016, offering precision-cut panelised prefab homes in Melbourne and surrounds. It works to a client’s existing design, and also offers a full design, project management and fitout service as required. The company’s system consists of timber-framed panels braced with oriented strand board (OSB), which are fitted with insulation, external cladding, and electrical and plumbing runs in the factory. “We use traditional, familiar materials, but everything is precision cut using automated CNC machinery,” explains CEO Sean Morley. “The very precise way that it all goes together means greater energy efficiency, fewer air changes per hour, and reduced heating and cooling needs.”
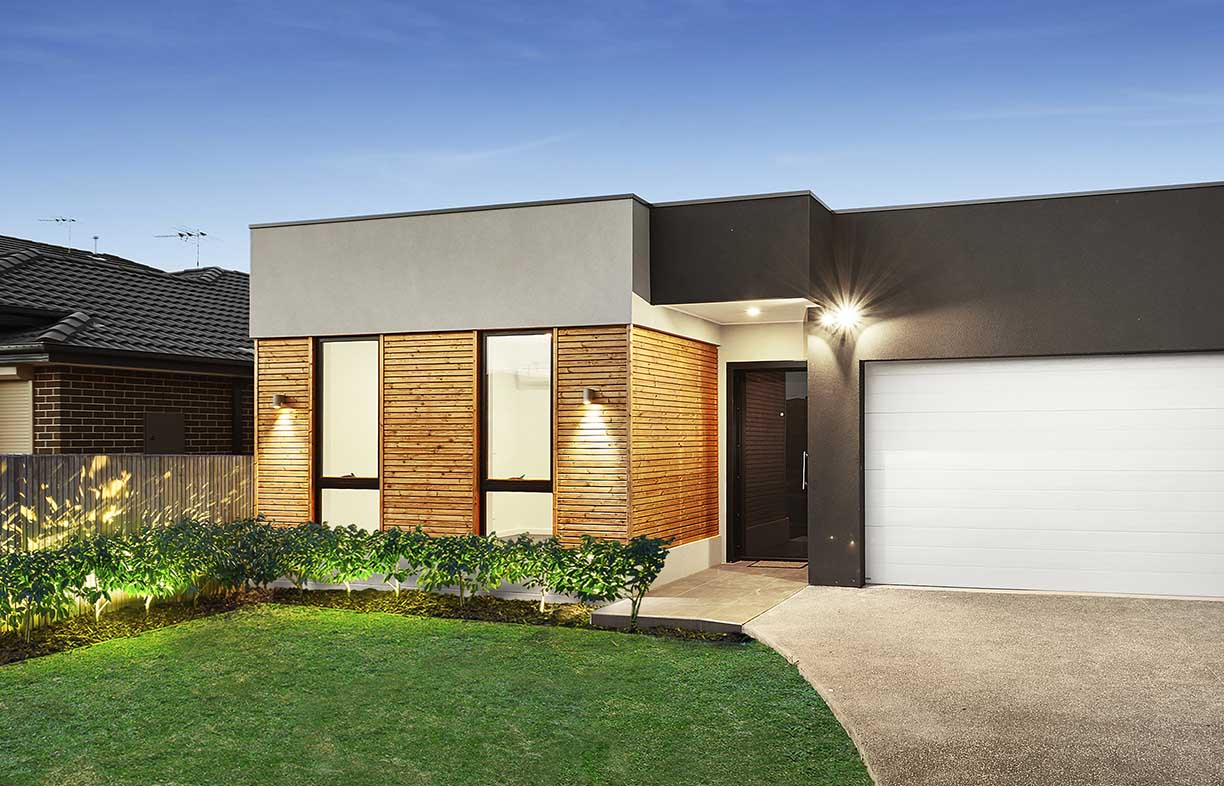
12. MAAP House
Hybrid modular/panelised construction system
MAAP House has been developed with sustainability and attainability as its primary objective. The firm aims to provide contemporary, high quality finished houses that can be built on any Australian house site. It uses a hybrid flat-pack modular system which it says is able to satisfy the broadest range of needs and accommodate aspect, budget and flexibility in floor plan designs and options.
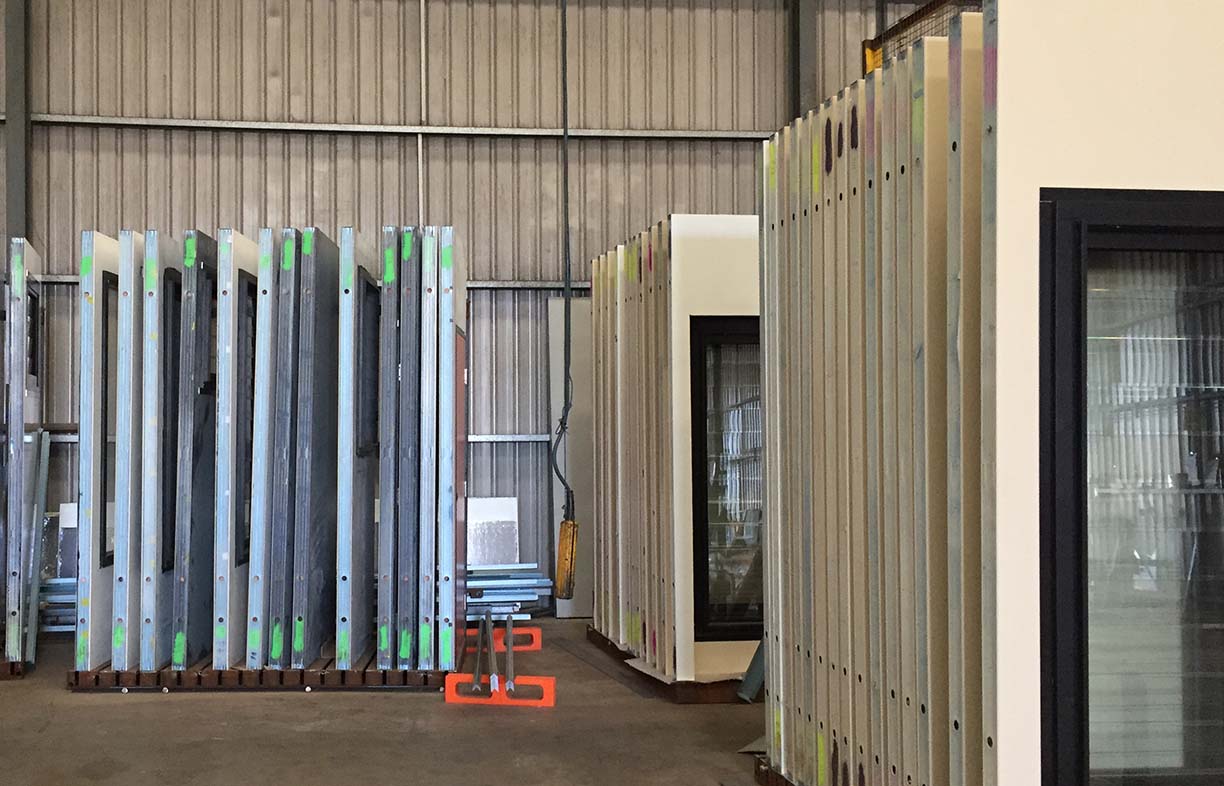
13. MODE Homes
Modular construction, folding assembly system
MODE uses a patented folding assembly system so homes are largely constructed in the factory, folded down for cost-effective transport and then folded back out when they reach site. The system was developed to reduce the prohibitive delivery costs associated with conventional modular construction.

14. Fairweather Homes
Modular and panelised construction system
Fairweather Homes has been delivering modular homes in Australia and overseas since 1982 and has constructed 400 houses to date. Its focus is architect-designed sustainable buildings using a “sophisticated” low-risk approach to affordable construction. Fairweather’s component-based, off-site fabrication uses locally sourced, low embodied energy materials.

15. Strine Environments
Modular construction, precast concrete
Architect Ric Butt of Strine Environments has developed over 30 years a new style of off-site prefabricated modular housing. The model integrates architectural design with precast concrete and environmentally sensitive construction to achieve climate-proof homes that provide an alternative to the usual lightweight, thermally poor-performing kit home products. The prefabricated modules have been designed to fit on a truck and can be delivered anywhere. The E-Cubed system uses Utility Modules and Space Modules to achieve flexibility.

16. Valley Workshop
Panelised construction system, polystyrene-free SIPs
Valley Workshop is a father-and-daughter team run by Penelope Haley with her father Warren French, the company’s principal architect. They employ a number of staff at their factory in Westbury in northern Tasmania and deliver across the state. The firm’s approach is bespoke and unique, manufacturing their own structural insulated panels free of polystyrene. The skin of the SIP and internal grillage system is made from Tasmanian hardwood structural ply, and wall modules are a stud frame built in the horizontal plane in the workshop.
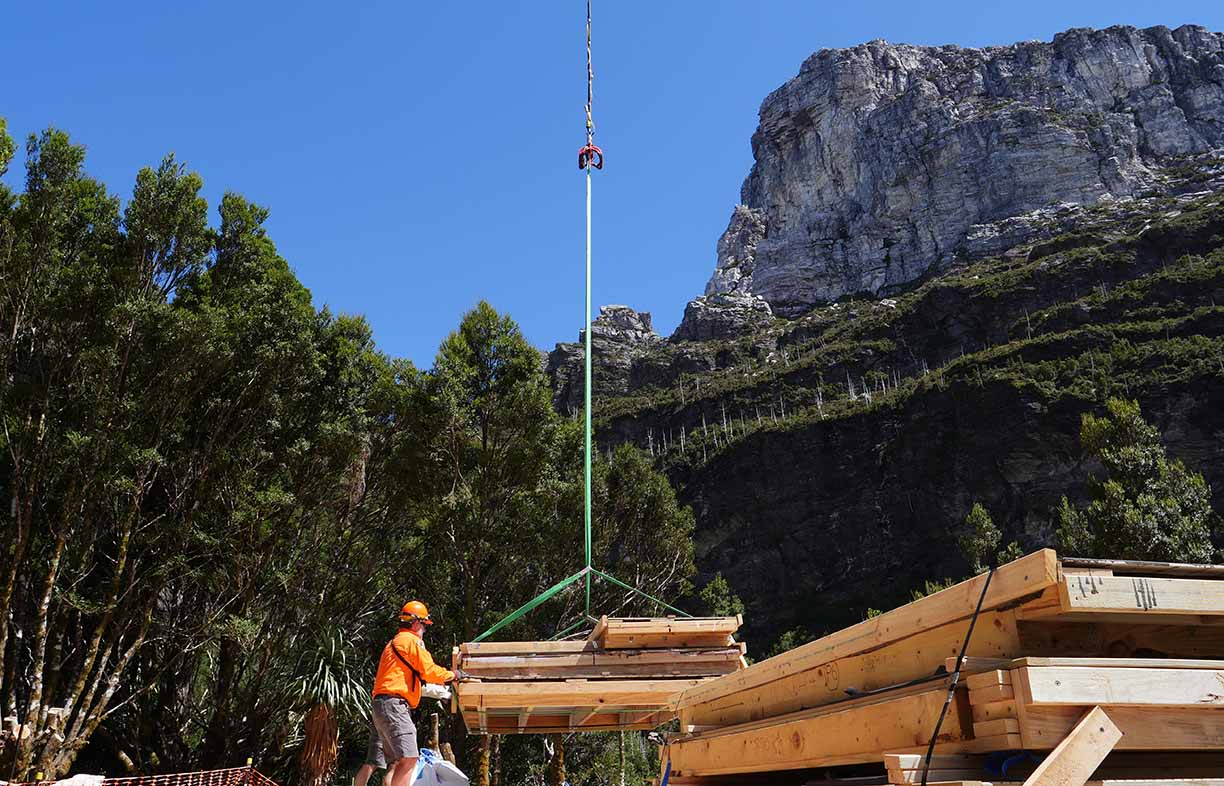
For further details on each company’s offering including price per square metre, construction time to lockup, and details of the projects pictured, please refer to the full 20-page special in Sanctuary 42.
More articles on prefab + modular design
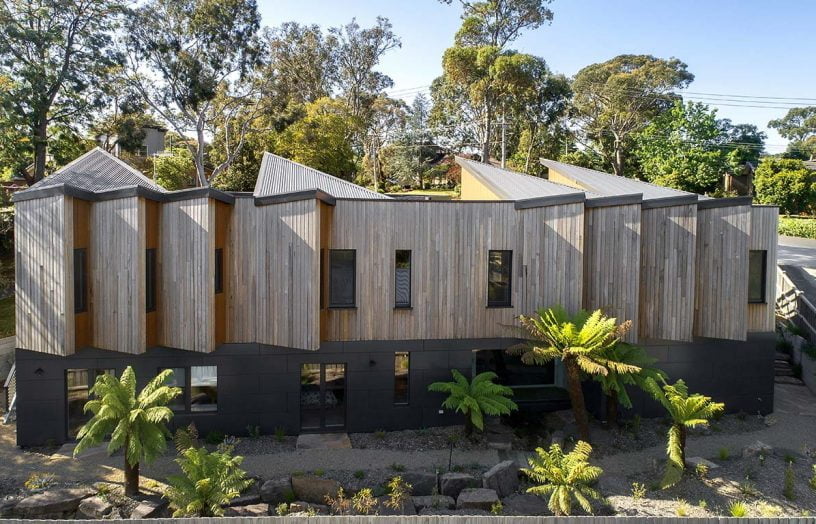
Outside the box
A Melbourne home pushes the boundaries of Passive House design, employing prefab panel construction to help break away from the typical boxy form to capture views and sunlight on a tricky site.
Read more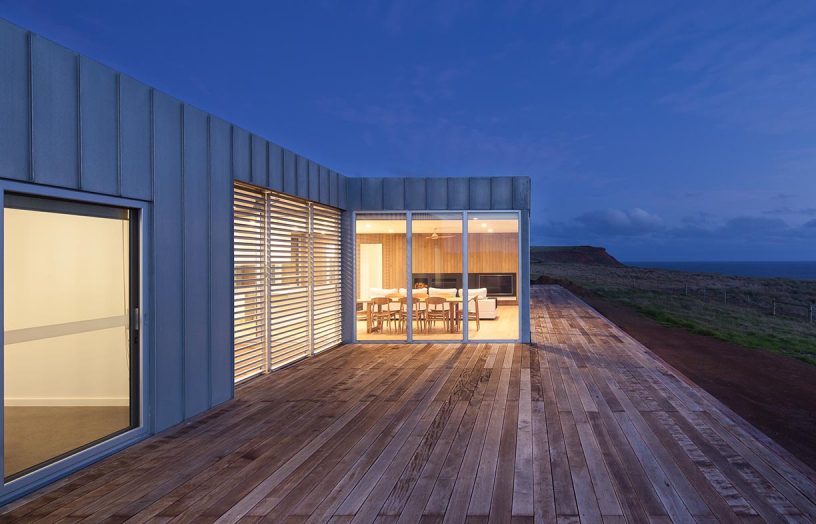
Sanctuary 42 out now – Prefab performers
Sanctuary 42 is out now, with a special feature on the latest developments in the modular & prefab industry in Australia.
Read more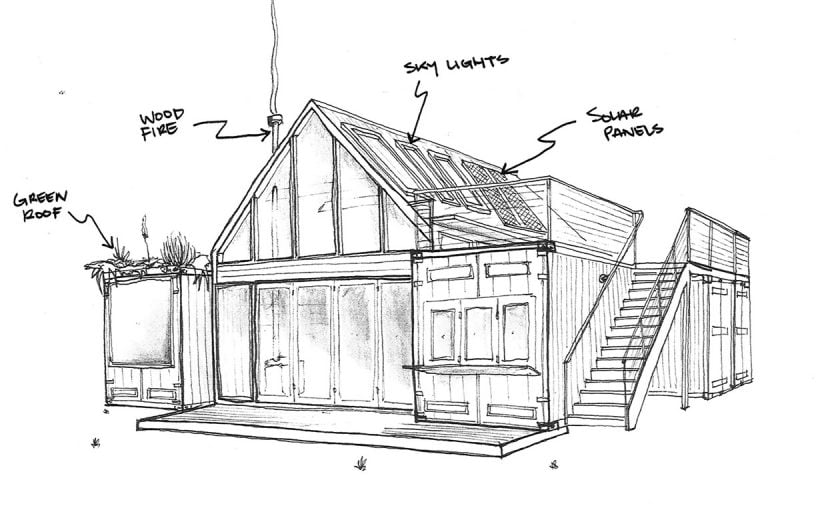
Design workshop: Modular mountain magic
A house designed around a series of modular units seems like a great solution for this holiday home in Victoria’s alpine region.
Read more
Modular and prefab homes around the world
From high-end, glossy affairs to inventive and economical buildings, here are a few fine examples of sustainable modular and prefab homes from around the world.
Read more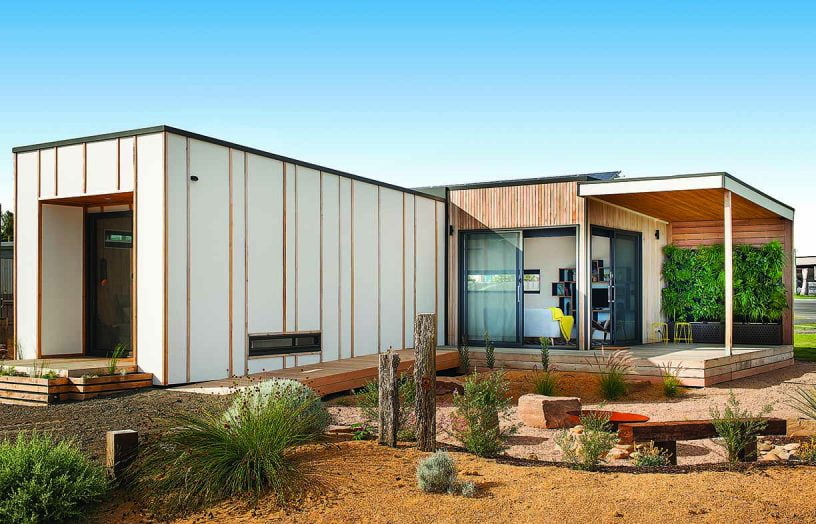
Twelve of the best modular and prefab creations
This article from 2015 is the first in our series of articles following the development of the modular and prefab construction sector in Australia.
Read more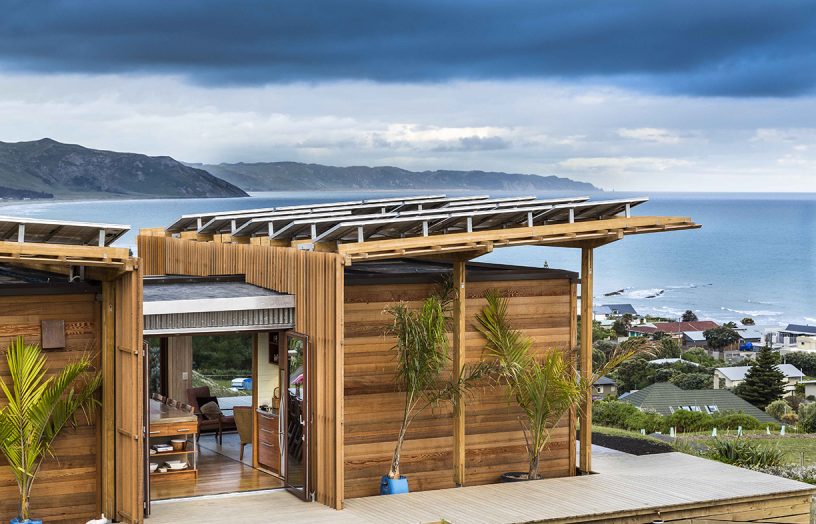
Kiwi bach
Designed as a student project for an international green building competition, this reimagined Kiwi ‘bach’ has found its permanent place on the east coast of New Zealand’s North Island.
Read more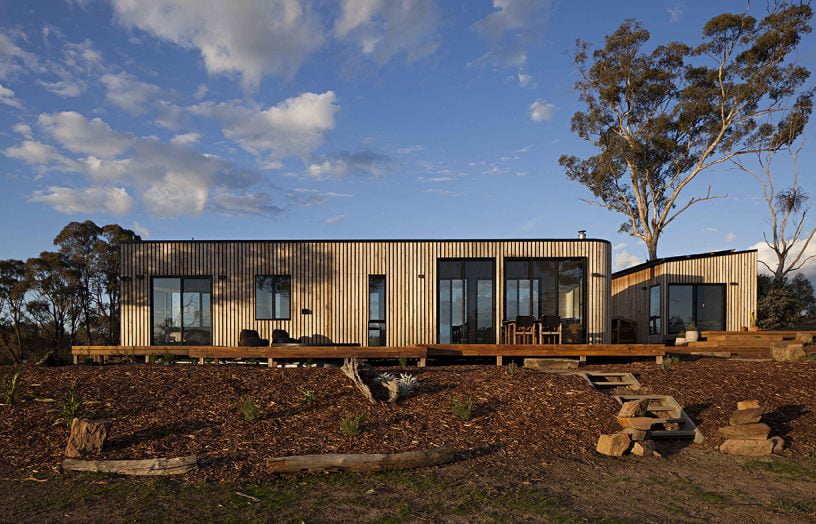
The ideal unwind
A prefabricated, modular design was found to be the most practical way for a Melbourne couple to build 130 kilometres away on a Central Victorian bush block.
Read more