When is a concrete floor the right choice?

Concrete floor slabs are a standard way to embed thermal mass in passive design, but is it always the right approach? Dick Clarke explains the benefits and design considerations for using concrete, and some alternatives.
For decades we’ve been sending out the message about thermal mass being a really useful way to achieve natural thermal comfort in a house, and concrete floor slabs are the most common way of doing just that.
Thermal mass is a term that refers to ‘enthalpy’, or any material’s ability to store heat energy. Enthalpy is actually a measure of any amount of thermal energy, so it can infer a relative excess of energy which we feel as warmth; or a relative lack of energy which we feel as the opposite, allowing the delightful term ‘coolth’ to make its presence felt. Think of it as a temperature flywheel.
As it happens, concrete is a brilliant material not only because it is strong, moldable and long lasting – it also has a lot of thermal mass. An important extra dimension is its conductivity, and these come together in passive solar design as follows: in winter the low angled sun penetrates the north-facing glazing, striking the top surface of the concrete floor slab. The conductivity of the concrete allows the heat to spread deep into its thickness, and the thermal mass absorbs it, gradually building up until the sun sets, when that heat is returned to the room. Then in summer, the well-designed building’s perfect shading angles exclude all sun, allowing the thermal mass to soak up any discomfort inside the house, whereupon it is dumped to the cool night air when the windows are thrown open after dark.
Except that it rarely works that perfectly. It’s not hard to spot the potential flaws in the fairy tale. Things that can and do often mar this perfect picture are imperfect building design, poor orientation, and uncontrolled shading. A neighbour’s trees or buildings, and other externalities, can also hamper our best-laid architectural plans. This design approach is also focused on localities with a cool to cold winter – north of the sub-tropical regions things are different. Additionally, most slabs won’t perform optimally if they are uninsulated; and yet, concrete floor slabs can still be of benefit, if designed into a holistic solution.
Thermal comfort benefits
Passive cooling
Because of its ability to soak up ambient heat, a well-shaded, well-insulated house will always benefit from thermal mass in hot conditions, as long as there is some low-energy means of dumping that heat. Traditionally, this meant night purging, which in spite of its horror-movie sound, is simply the practice of opening up windows and doors in the cool evening to allow the heat to escape.
If there is no reliably cool evening, such as in Darwin, Broome or Cairns, thermal mass may not be useful in that way. Some climates allow mechanical cooling of the slab, such as hydronic cooling, but in humid climates condensation is a risk unless the building is sealed and air-conditioned.
Passive solar heating
In regions with cooler winters, using orientation to admit winter sun deep into the building is key to making the thermal mass in a concrete floor work. If no free solar energy is available, the slab will not heat up and will instead act as a passive cooling heat sink just when you don’t want it to. This is an all-too-common experience and has given concrete floor slabs a bad name in some people’s minds.
You can also use solar energy ‘borrowed’ from somewhere else to heat the slab, usually from the roof of the house using electricity and water to transfer it: solar hydronic heating. You can also use a combination of both approaches where there is some solar access but it is insufficient.

Ground coupling – or not
An uninsulated concrete slab on the ground will, if the building above is well insulated, draw up deep ground temperatures from about three metres down. In many parts of Australia this gives the slab an annual temperature range of about 16 degrees Celsius in late winter to spring, ranging up to about 19 degrees Celsius in late summer to autumn. While a bit too cool for comfort, at least it’s a stable starting point. Passive solar design will provide free solar gain from north-facing double glazing to add approximately four to six degrees to the slab in winter taking it within the perfect comfort zone. Passive cooling is then used to exclude any summer sun to allow the slab to hover in the comfortable 20 to 22 degree range well into late summer.
The more southerly and higher altitude regions have soil temperatures that are too low for this to work well, and under-slab insulation is called for. Also, if external factors prevent solar access, insulation may also be a good idea. Slab edge insulation is always a good idea. This is because the ground temperatures at the surface vary wildly, directly affecting the perimeter of the slab. Note that waffle pod slabs, originally designed to act like stiff rafts on highly reactive clay soils, act like insulated slabs. The big and burning question is when to insulate, and when not to? Local knowledge from skilled professionals is the key here.
The bigger picture: total eco-impacts
The ultimate goal of using thermal mass is to help create a comfortable, long-lasting home. So any concrete floor slab should pull its weight in the contest against discomfort, by eliminating or seriously reducing heating and cooling energy. But there is more to the energy equation than just what it will save during the building’s operation: there is the energy it took to make the concrete; the energy that it will take to remake it at end of life; and the other social and eco-impacts of that making and recycling. This is called a life cycle assessment (LCA).
The major pollution byproduct of conventional concrete is the carbon dioxide emitted during the production of Portland cement, but other emissions occur during the quarrying of virgin sand and aggregates, transportation, and curing. The quarrying itself has a major impact, including large holes in the ground, noise and trucks on the road.
Compared to some other materials, concrete is starting from a less desirable point and should be used in ways that reduce its ecological debt. This can be by maximising its operational benefits during the building’s life, and minimising its eco-impacts at end of life. Key to that is ensuring the building is designed and built well, and has a long operational life. The relentless redevelopment of our cities can make the future of a building an uncertain one – a fact to consider seriously.
To assist designers to make good product selections, the Building Products Innovation Council created the Life Cycle Inventory database of the most common building materials and products. It shows that 20MPa concrete (common low-to-moderate strength, can be used for slabs on stable soils) has a carbon debt of 1.62kg per kg of concrete produced, whereas 40MPa concrete (common high-strength, used in suspended slabs) has a carbon debt of 2.36kg per kg – a 45 per cent increase. Engineers therefore need to find a balance between the added carbon debt and the potential increased longevity of a slab that uses higher strength concrete.
Another little-known impact of concrete is the affect its high alkalinity has on aquatic life forms. Although most floor slabs are internal, and not exposed to the rain that then becomes run-off to creeks some outdoor slabs are within the hydrological cycle. Concrete can raise the pH levels of waterways which can affect their health, but stormwater systems are the main culprit in this regard.
Innovations here and on the horizon
There are ways of reducing both the carbon debt of concrete and its quarrying impacts. The use of ‘extenders’ – other low-carbon materials that displace some of the high impact materials – is well proven.
Flyash, a byproduct of coal-fired power stations and steelmaking, is used to replace various amounts of Portland cement. It is a kind of geopolymer, and it is standard practice for many designers and engineers to specify 25 per cent replacement, in such products as Boral Envirocrete. But Boral has taken it to another level with their Envisia concrete, reducing its carbon debt by a whopping 65 per cent. It is currently available only from a few of their many depots, but demand will see that become universal – so start demanding! We have used Envisia and found it to be workable for a longer period than conventional concrete, with less shrinkage and creep. Of course, as we phase out coal-fired power, these waste materials will become scarcer, and truly long-term alternatives will need to be found.
The Sustainable Resource Centre at Sydney’s Fairfield City Council has teamed up with Metromix’s Wetherill Park depot to create a 95 per cent recycled concrete (by volume), using recycled sand and aggregates in concretes which can be specified up to 42MPa – even the mix water is harvested on site. Depending on the source of the sand, this mix has a slightly different colour to conventional concrete and stays workable for long periods.
Low-carbon and carbon-neutral geopolymers provide a complete alternative to Portland cement, with dramatically lower carbon emissions during production. Some even absorb carbon dioxide during curing, enabling the concrete to immediately repay some of its carbon debt. For over 20 years, Tasmanian company TecEco has been developing and researching low-emissions magnesium cements that can absorb carbon dioxide during curing, but these are not yet widely or commercially available.
Design considerations – rules of thumb
Where to use it?
The default starting point should be to use concrete floor slabs where it can help provide free heating and cooling: where good solar access is available, concentrate on the northern zones of the home. This can be extended to other zones if you include low-energy heating systems like solar hydronics, which will still take advantage of the thermal mass.
How much concrete?
It’s possible – easy in fact – to have too much. This will overpower the heating cycle and become a heat sink. Generally, floor slabs work well even if the rest of the building is lightweight.
Which concrete?
Speak to your designer and engineer about not over-specifying the strength. This is often done because engineers don’t trust builders to cure concrete properly – and sadly they are mostly right! Controlled curing will bring concrete up to 95 per cent of its ultimate strength in 21 days, and can be done by applying a curing compound, or covering with plastic. Wetting uses too much water, as it should be applied continuously for two weeks, and potentially up to a month.
Should it be insulated?
Generally, if there are extremes of temperature for more than several hours per day for several months of each year (that is, most of Australia), then the edges should be insulated. Insulation beneath the slab is a more nuanced question (refer to the yourhome.gov.au website for more details than I have space for here). If any heating system is installed, the slab must be insulated as required by the building code.
What about the first floor?
First floor slabs need a bit of careful thought. If the living areas are upstairs, with an ability to effectively isolate the two levels (that is, doors near the stairs), then a suspended slab will provide all of the passive design benefits described above. If, however, the bedrooms are upstairs, and especially if there is no effective way to isolate the two levels, or no way for the upstairs to freely vent heat all day in summer, then the upper slab may accumulate too much heat and make bedtime quite uncomfortable.
What about installing services?
It is self evident that adding services to a completed concrete slab is problematic, so good planning is essential. Make sure all plumbing and electrical and other services are installed during the preparation phase.
Aesthetics – finishes and colour
Concrete can be supplied with noticeably different colours and aggregates. Exposed surface finishes generally fall into two camps: burnished or polished.
A burnished finish is achieved by simply trowelling the setting concrete until it literally shines. This process can be done by hand, but more easily by powered ‘helicopter’ machines that are used to give the slab its smooth, steel-trowelled finish. This process may extend the trowelling by several hours. On completion, the slab must be protected from impact and scratching for the duration of the works. The surface is left with a natural looking mottled finish, which can be further enhanced by staining, then sealing.
Polished concrete is a slight misnomer – it actually means to grind the surface back several millimetres and then polish. This exposes the aggregates, which may be specially selected for size and colour, including small pieces of glass, sea shells and other small articles. It may also be stained, but more commonly oxides are added to subtly alter the colour of the background. The grinding and finishing is usually done late in the building works, but even so, the surface is usually protected to prevent any deep damage.
The surface of a slab can also be sand blasted or acid washed to etch to varying degrees. All material washed off the surface must be contained and removed, rather than allowed to wash into the outside world.
The surface isn’t just something you look at – you walk and perhaps even sit on it too. Concrete is by definition quite hard. Consider whether work areas, like the kitchen, need a softer surface so you can stand comfortably for long periods; it also gives that wineglass a second chance.
Alternatives
It is always easiest to go with the flow in decision making. But you should ask questions at every stage of planning a project: is this the best material for the job? Are there alternatives that might do it better? Any material with valid credentials will survive this questioning and give you confidence in the choices you have made.
The traditional alternative to concrete slab floors is the conventional raised timber floor: timber flooring on bearers and joists on stumps. In many situations this is a valid choice too, such as on steep sites, or where there is no solar access and thus no free heat to soak up.
But there are hybrids too, offering the best of both worlds: thin suspended concrete on bearers and/or joists, seen in systems such as Smartslab. This has a moderate amount of thermal mass, and while it may not be quite as soundproof as a full slab, is generally quieter than a timber floor. CSR Hebel also makes lightweight reinforced precast concrete floor panels, which can be laid very quickly over timber or steel structures, but the surface cannot be exposed, needing either a topping, tiles or carpet.
An alternative to providing thermal mass in a lightweight floor structure is to use phase change materials. These change between solid and liquid at room temperatures and absorb or release large amounts of thermal energy as they do so.
Recommended for you

Tradies and the transition
Do we need as many tradies for electrification as many think? Not if we are innovative, writes Alan Pears.
Read more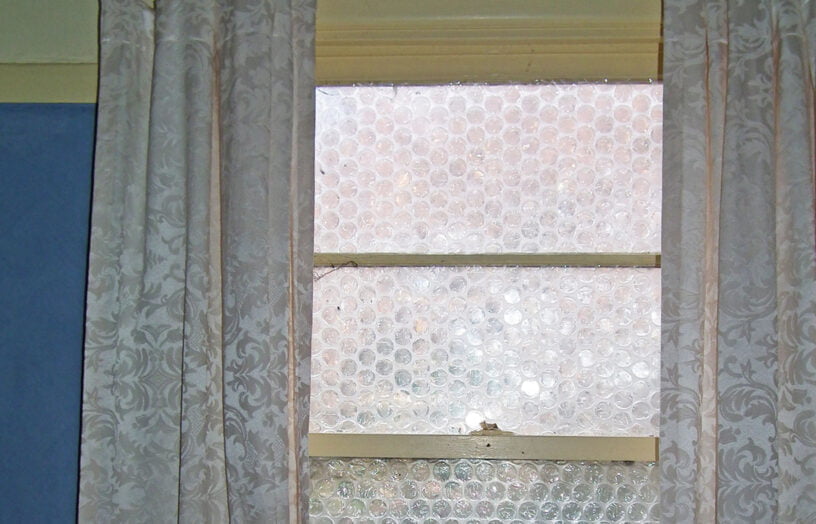
Double glazing on the (very) cheap
Do we need as many tradies for electrification as many think? Not if we are innovative, writes Alan Pears.
Read more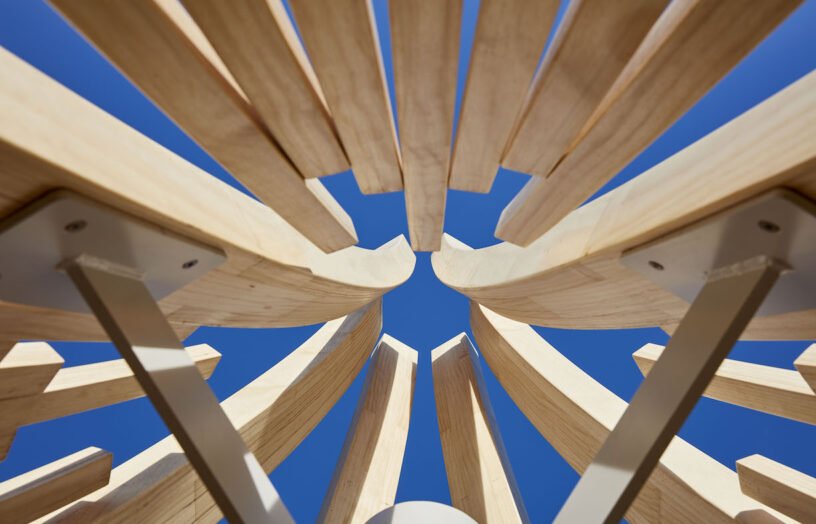
In praise of Accoya
Native hardwoods are beautiful, strong and durable, but we need to wean ourselves off destructive forestry practices. Building designer and recreational woodworker Dick Clarke takes one hardwood alternative for a test run.
Read more