In praise of Accoya
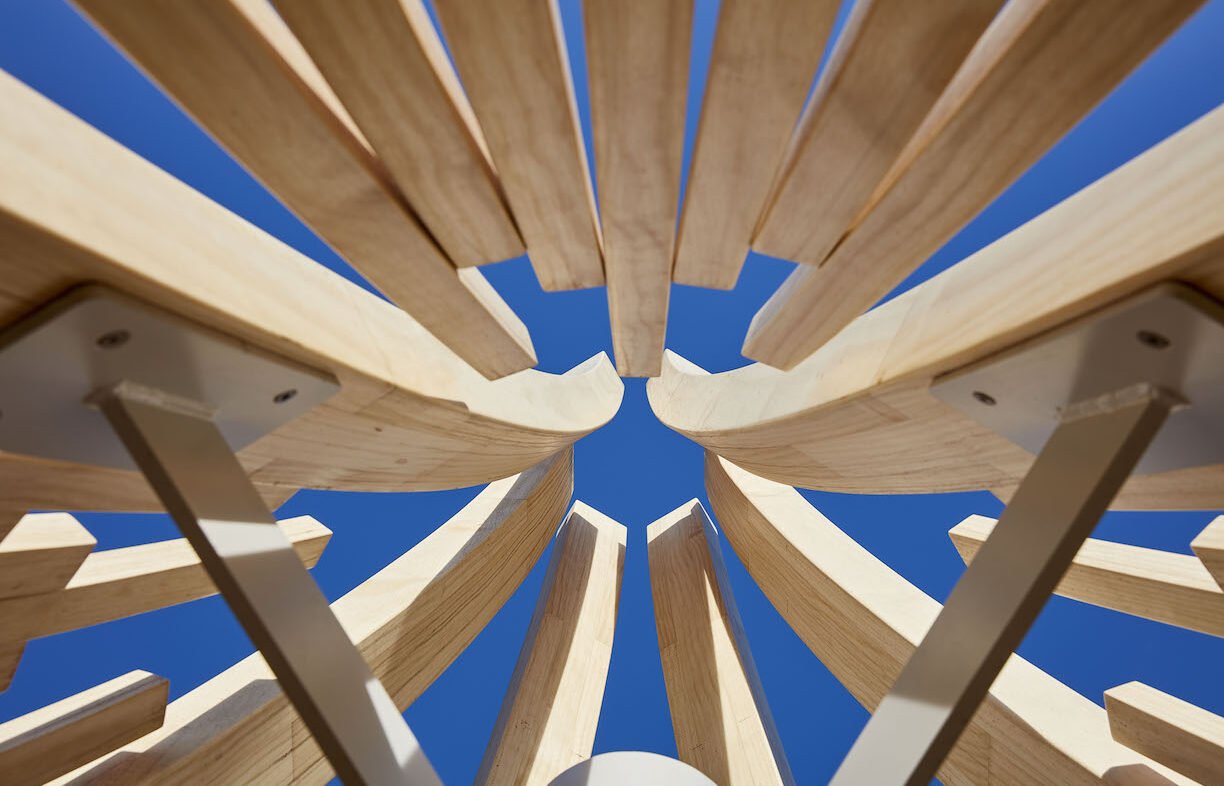
Native hardwoods are beautiful, strong and durable, but we need to wean ourselves off destructive forestry practices. Building designer and recreational woodworker Dick Clarke takes one hardwood alternative for a test run.
The world has used and loved Australian native hardwoods for over 200 years, with such faraway structures as the London docks benefitting from the material’s longevity in arduous conditions. However, as a result of sustained logging, land clearing, bushfire and now climate change, our forests are in a bad way and our koalas and other fauna have a less than ideal run at life.
Partly as a result of the devastating 2019-2020 Black Summer bushfires, most states have recently restricted or stopped altogether the logging of old-growth forests (as opposed to plantations). Many would argue that this is too little, too late, but most agree the time has most definitely come.
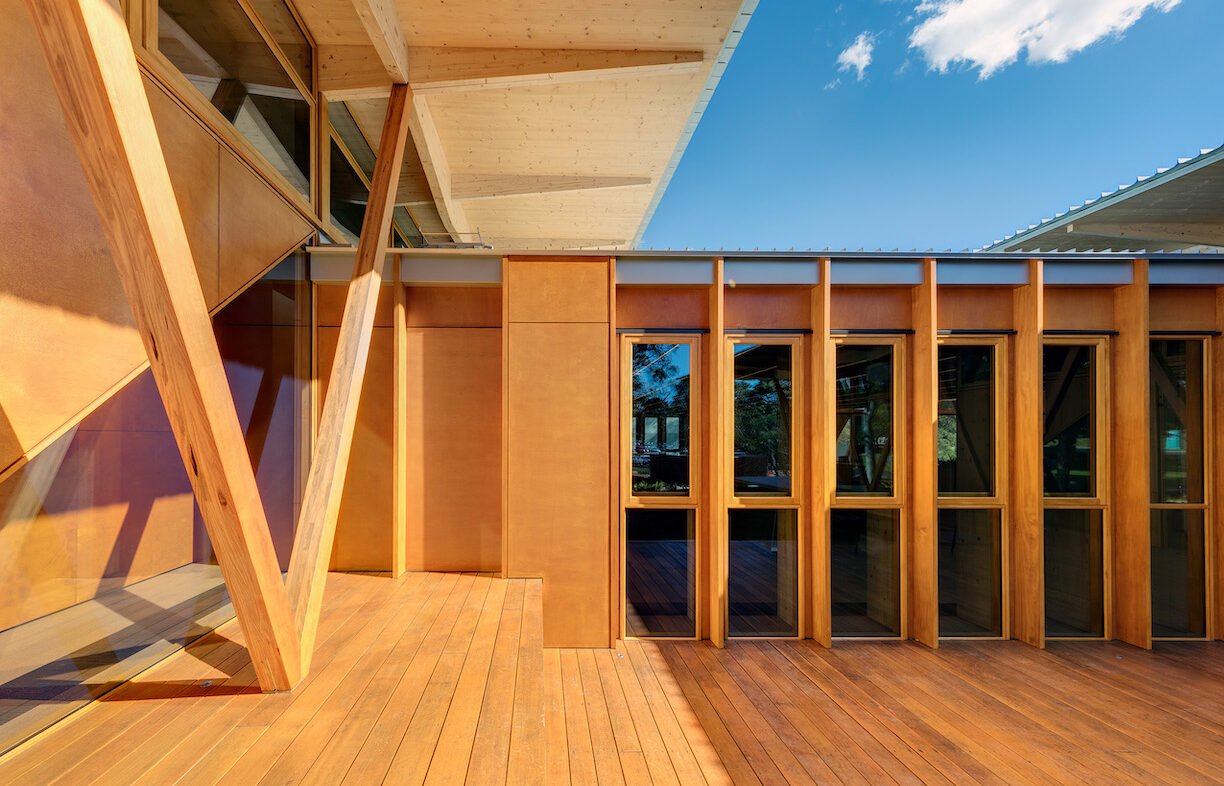
Luckily, there are now alternatives to old-growth hardwoods that are as good or better performance-wise, and have lower ecological impacts. One such solution is Accoya: a very different kind of treated pine that can replace hardwoods in many applications. Before we explore its potential, though, let’s remind ourselves of the characteristics native hardwoods are valued for, and that any really useful alternative will need to match up to:
1. Strength. With a stress grade of F42, ironbark is around six times stronger than typical framing pine (MGP10 – machine graded pine able to bear pressure of 10,000MPa; equivalent to F7). Ironbark is a standout, but even lesser hardwoods are usually in the F17 to F34 range.
2. Stability. Many softwoods, and especially pine (Pinus species), are susceptible to moisture ingress. Because their grain structure is open, any ambient water vapour or liquid water can cause the timber to grow across its cross section. Variations in density can lead to different movement within even short lengths, causing twisting and bowing. Hardwoods are not immune from this, but most are more stable once properly milled and dried.
3. Longevity. Most hardwoods have good resistance to insect attack, especially from termites, setting them apart from nearly all softwoods. (Cypress pine (Callitris species) is the softwood exception: once Australia’s ubiquitous flooring and cladding timber, it has exceptional resistance to termites.) Resistance to fungal decay (rot) is another feature of many hardwoods, making them suitable for external use. Ironbark and Huon pine are rated Class 1 for durability, while untreated pine is only Class 4.
4. Fire resistance. In residential applications, bushfire is the main fire risk we have to design for, and for the most part that means embers causing ignition on exposed surfaces. The relevant standard AS3959 Construction of buildings in bushfire prone areas contains a list of hardwoods (six out of seven being native hardwoods) that have been tested to resist ignition when exposed and uncoated, up to a Bushfire Attack Level of BAL-29. (That is not to say they are fireproof, as some intervention is assumed in that standard; my own experience has shown that even ironbark will ignite if left in a dense ember shower with no intervention.)
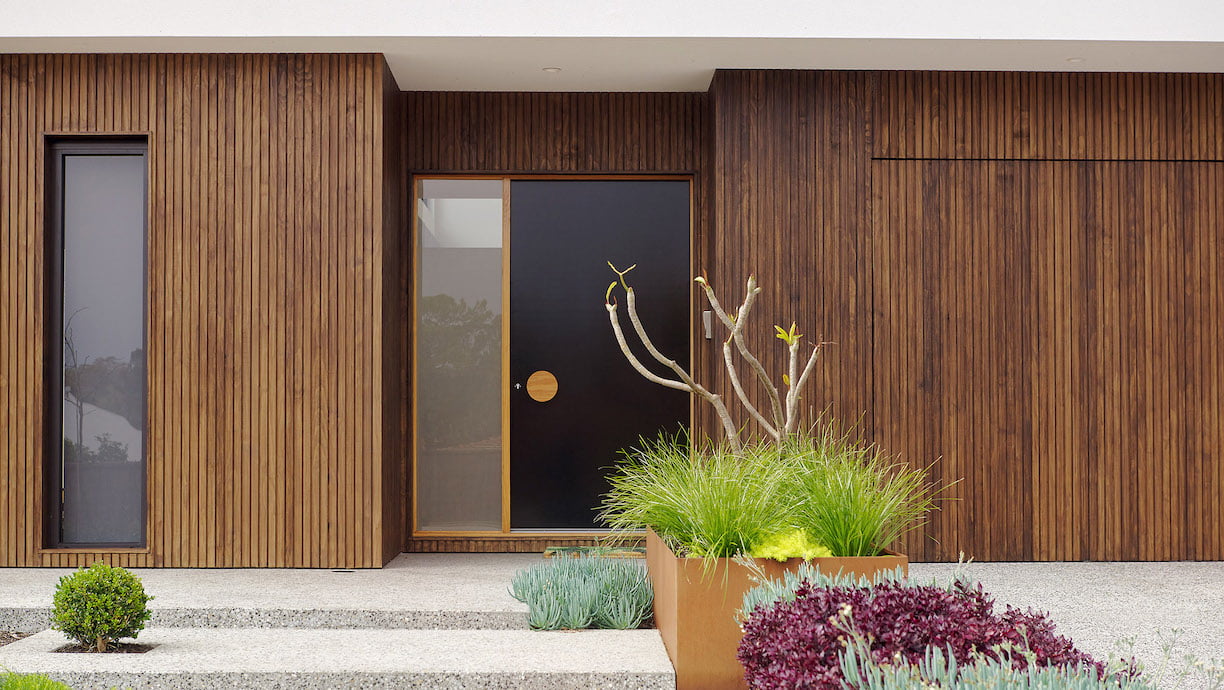
Accoya promises to be a very good alternative to hardwoods in most applications not requiring unprotected fire resistance. It starts life as plantation radiata pine grown in New Zealand (because the climate there is great for growing big fat pine trees quickly, that are very straight and largely clear of knots). The pine then undergoes treatment in the Netherlands to transform it from Class 4 for durability to the very top of Class 1 – possibly pipped for supreme champion only by Huon pine, that rare and much-revered boatbuilding timber from the wilds of the Tasmanian west coast.
The technical name for the apparently magic treatment that produces this transformation is acetylation, and it’s actually fairly simple in principle: the pine timber’s cells are pumped full of a type of vinegar, which makes them impervious to external moisture. Don’t use this vinegar on your chips though – it’s a bit too strong for human taste buds! It is acetic anhydride, and it catalyses the acetylation process, interacting with the wood molecules to make them resistant to binding with water. The vinegar does not remain in the finished Accoya product, and once the process is complete it can be used in other industries, or reprocessed for use again in the acetylation process.
Unlike more traditional H2 and T2 perimeter treatments used for most pine framing timber these days, Accoya’s acetylation treats the timber all the way through, and it avoids the use of toxic chemicals. The result is real non-toxic wood that doesn’t rot, warp, swell or shrink, resists splintering, and is inedible to termites. It is so dimensionally stable that it’s perfect for painting, and has outstanding durability. The process adds a small amount of strength and hardness to the original timber, but this should not be overstated.
Suitable applications for Accoya include pretty much anything you would use hardwood for (or softwood, for that matter) that does not require uncoated fire resistance: decking, cladding, joinery for windows and doors, fencing, boatbuilding, even large-scale timber artworks. It also comes in an optional ‘pre-aged’ finish, Accoya Grey, which I think looks fantastic in exposed decking and cladding applications.
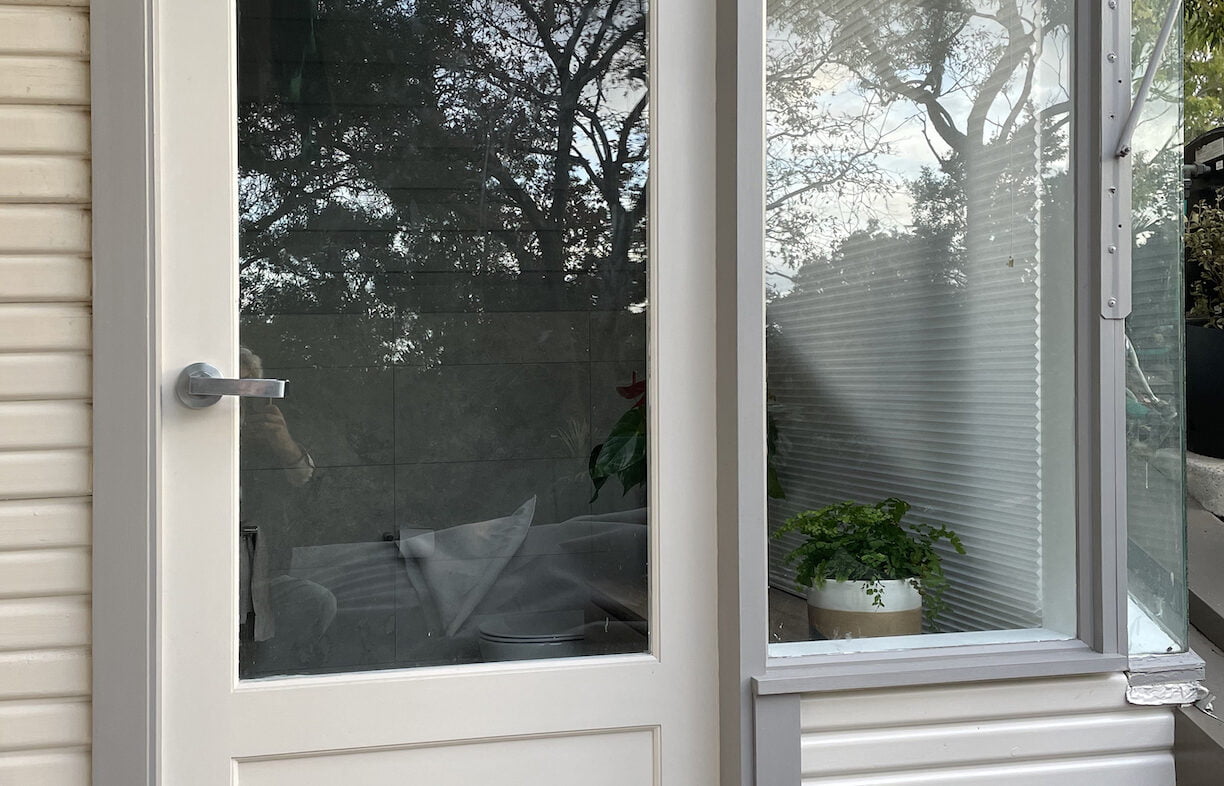
Putting Accoya to the test
Because I like to try materials out myself before unleashing them on clients, I undertook two small projects with Accoya: a new window and door unit with a high degree of weather exposure, and a new cabin on a 65-year-old timber boat.
The window and door unit was made for me by fellow Accoya enthusiasts H2 Custom Joinery in Warriewood, New South Wales. They like its machinability, its dimensional stability, and that fact that it takes coatings (both painted and clear) so well. Owner Nick Harley also introduced me to the MDF version of Accoya, cutely named Tricoya. He has had a piece lying outside his office in full sun and rain and in contact with ground moisture for many months, and it has not swelled or changed dimension to any extent that he has been able to measure – a pretty impressive result. So we used Tricoya as the solid panel in the bottom section of the door. After six months of sun and rain, the newly installed door has not swelled or shrunk at all.
The boat cabin was part of a larger project to restore my little timber launch and upgrade it from a diesel engine to an electric motor with solar panels. The old half-cabin was not the original, didn’t suit the graceful lines of the hull, and certainly did not provide enough area for solar panels. So I drew on my long-past naval architectural training and designed a whole new cabin using Accoya framing and hoop pine plywood (in the absence – as yet – of an Accoya ply product).
I found the Accoya easy to work with. It machines well, often coming off the fine rip saw needing only a light sand before painting. The thicknesser predictably produced a very fine surface finish. Laminated curved cabin-top beams were produced easily using bio-epoxy, and are very stiff and stable. (Any epoxy will do, but bio-epoxy is made from canola oil rather than fossil oil, so – why not?)
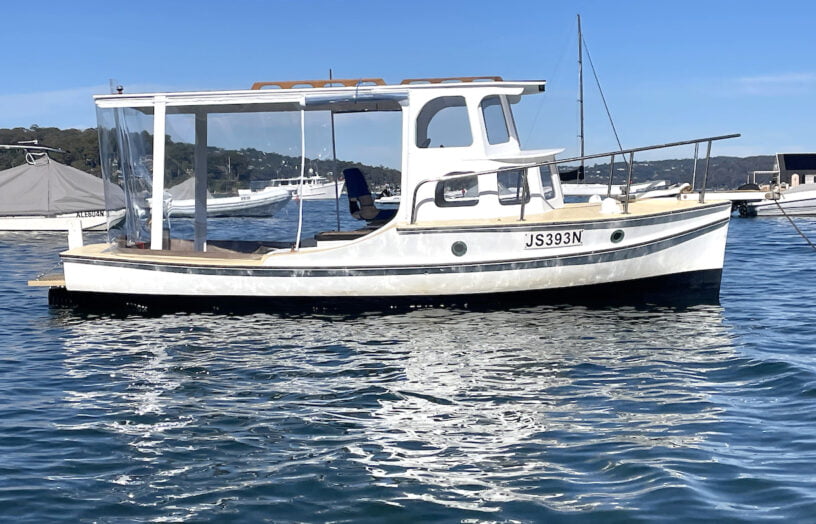
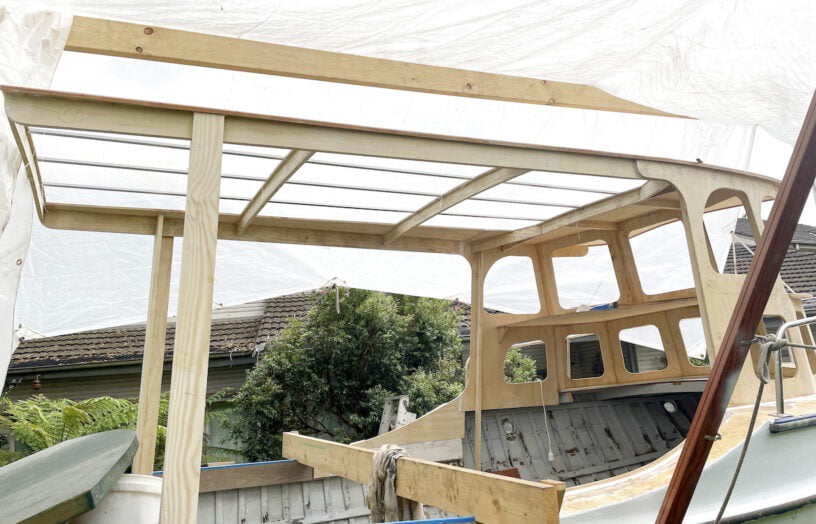
Where next for Accoya
Having satisfied myself that Accoya is a perfectly viable alternative to hardwood in many applications, I wanted to understand why it’s made by sending Kiwi timber halfway around the globe to Europe for treatment, then bringing it all the way back again. The local importer and distributor in Sydney is Britton Timbers, and their manager Anthony Long explained that so far Accoya is still seen as a boutique timber, specified only in very limited volumes. Producing the product locally would involve an investment of a few million dollars in the necessary equipment, which would easily be justified if the sales demand is there.
I suggest that the recent moves to end old-growth native forest logging, and the fact that Accoya is cheaper, stronger and more stable than timbers like western red cedar, that old staple of the joinery trade, means that its time has come. Get specifying, architects, designers and builders! The investment in the plant is no major obstacle if we drive enough demand. The koalas will thank you.
My final word is to our governments: we need to support the erstwhile logging communities to transition to a sustainable economy. Towns like Millgrove in Victoria are showing how the transition can start, with the local council and the Minderoo Foundation collaborating on transition and resilience building. This kind of hands-on resourcing is needed in all of the affected communities across Australia, so the tree fellers and truck drivers become part of the drivers for a sustainable future. The koalas will thank them too.
Further reading

How energy efficient is the house you are buying or renting?
Victorian renters need stronger minimum energy standards. Read Renew's submission.
Read more
ACT looks to expand rental standards for energy efficiency
Victorian renters need stronger minimum energy standards. Read Renew's submission.
Read more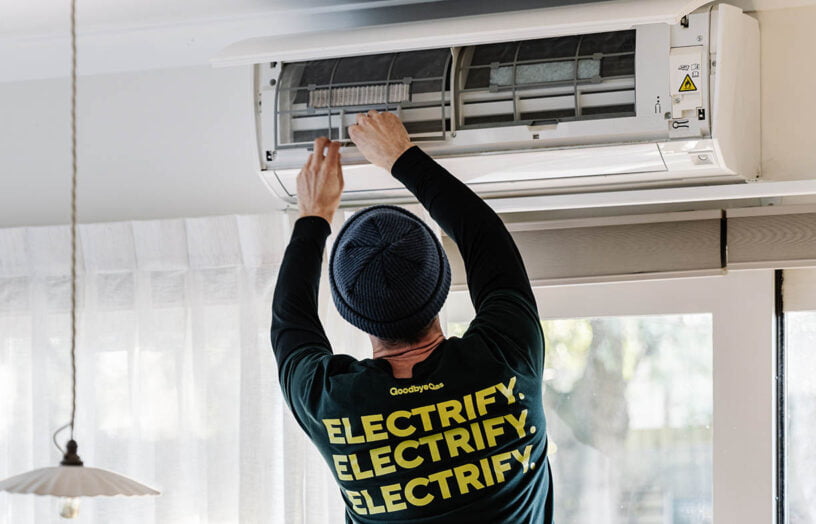
All together now: One-stop shops for energy upgrades
If you want to do a home energy upgrade, it can be hard to know where to start. One-stop shops offer advice, information and referrals all in one place; we take a look at what they’re all about.
Read more