Building without the waste

Construction waste is a huge problem, with vast quantities of materials, both old and new, going to landfill each year. Sophie Weiner examines the problem and what can be done to fix it.
For the last two decades, Australia has been amid a construction boom, with over half a million homes built across the country. Now, as the residential construction slows down, infrastructure is ramping up, with $100 billion in infrastructure spending promised over the next 10 years. And though housing construction has slowed down, there were still over 200,000 new apartments and homes built each year since 2014, according to the Housing Industry Association.
While the ongoing construction mania may be a boon for Australia’s economy, the wave has downsides for the environment. According to the 2018 National Waste Policy report, 20.4 million tonnes of waste are produced by the construction and demolition industries in Australia every year. That’s nearly a third of all waste produced in the country. And the problem is growing: from 2006 to 2017, the amount of waste produced by the construction and demolition industries increased by 20%.
Most of this waste comes from large-scale projects, including infrastructure and construction of large commercial and multi-residential buildings. But even in constructing single homes or undertaking renovations, a huge amount of unnecessary waste is generated. Though 67% of construction waste is eventually recycled, that’s still 6.7 million tonnes of waste ending up in landfills each year. Much of that waste is perfectly useable product in the form of offcuts and over-orders.
This article looks at the scope of the problem and its solutions, from the perspective of both homeowners and other industry stakeholders. We consider the roadblocks the construction industry faces if it is to reduce its waste, and the opportunities for change. It’s still a long road to a waste-free building industry, but with commitment and creativity, there are strategies we are sure could help us get there.
Reviewing the problem
Why is it so difficult to reduce waste on construction sites? A lot of it comes down to the fragmented nature of the industry, says Nilupa Udawatta, a lecturer of construction management at Deakin University who studies construction waste and how to reduce it. Udawatta says that people who engage builders often find they have little influence over what happens on a building site.
“In the traditional arrangement, there is a lack of coordination or communication between builders, contractors and subcontractors, so it’s hard to implement [waste management plans],” says Udawatta.
Even if the builder and contractor agree about waste management practices, subcontractors working on the site may still flout these agreements.
On larger projects, like those run by the government or major construction companies, waste streams can be separated in different bins, which Udawatta says is the best way to ensure that materials are recycled. Building sites may have a bin for concrete, one for metals, one for plastic, etc. But on smaller sites, especially those in cities, there’s often not enough room.
“Most residential projects end up putting all the waste in one bin,” Udawatta says. “This can cause contamination, which can reduce the possibility of reusing those materials.”
Changing attitudes
Udawatta says that culture and attitude also play a major role in preventing progress. “One of the most important barriers to reducing waste is resistance to change,” she says.
There is a debate within the community interested in sustainable building about how to best go about changing these attitudes. Udawatta says that strict government regulation doesn’t always work as well as people assume. In Hong Kong, higher landfill costs helped to reduce waste for a while, but eventually led to illegal dumping. This problem exists in Australia as well, where some recyclers have been found to be stockpiling dangerous toxic materials rather than paying a fee to tip them.
Due to these complications, Udawatta says she believes financial incentives work better than government mandates, especially in a competitive industry where many builders are just trying to survive.
“We need changes in attitude and behaviours of people,” she says. “There should be an economic benefit to reducing waste.”

Strategies to reduce waste
There are already quite a few options for people looking to reduce their waste output on building projects. Recycling companies like BinGo, Mobius and Instant Waste provide bins to construction sites, big and small. All waste is placed in one bin, which these companies then sort at their own processing facilities.
Representatives from BinGo told Renew that the company tries to recycle at least 75% of materials they collect, while Mobius said it aims for a floor of 80%. Both companies say they often recycle close to 95% of the materials in their bins.
At the BinGo recycling facility Renew visited in West Melbourne, trucks loaded with bins waited in line to dump their waste into a large warehouse, where a preliminary sort is done. Heavy materials like bricks and dirt are placed on one side, while lighter materials like timber and plastic go on the other side.
From there, the materials are loaded onto a conveyor belt to be sorted by employees. These sorted materials will be used to make recycled products which the company sells. Some products, like the road base made of crushed rock, are made on site, while timber is sent off to a contractor to be made into mulch.
BinGo’s Melbourne plant operations manager Ben Morgan says the company aims to create products equal to any others on the market.
“Once you see that good product you say: that’s not waste, that’s stuff that people genuinely want,” he told Renew.
These companies also provide reports to their customers on how much of the waste was able to be recycled, which can help builders reduce waste. Some builders may not even realise the ways in which they could easily reduce waste and save money on materials until they know what’s being put into their skips.
“If a builder has too much waste, there are two reasons: either they’re not managing the site very well, or their ordering department is over-ordering materials,” Mobius sales and marketing manager Karen Barbin says.
Ideally, these companies will help create an economy where using recycled products are the norm.
“I love to go out to our processing facility in Sydney—you see these huge trucks driving in with waste and the same trucks driving out with product,” Yeena Kirkbright, BinGo’s communications manager, says. “You can see the circular economy happening right in front of you.”

Reuse or recycle?
Companies like Mobius and BinGo divert thousands of tonnes of waste from landfill every year. But sustainability experts say their methods are still inferior to separating streams of waste for recycling, or better yet, simply using the quality materials that are often thrown away.
Sustainability Victoria’s 2018 Statewide Waste and Resource Recovery Infrastructure Plan suggests methods that would allow more construction waste to be reused in its most economically beneficial form. Instead of downcycling cast-off timber into mulch, the plan suggests creating different categories to denote the quality of recycled timber. Some timber considered waste by builders is strong enough to become a structural element, while other timber offcuts could become non-structural elements.
“Downcycling is better than sending materials to landfill,” Udawatta says. “But we don’t have unlimited resources. If we downcycle, there will be a point where we have to extract more resources.”
Udawatta says the most important aspect of this strategy is convincing builders that they can trust recycled materials and creating a market for those materials.
“Some people don’t like to use recycled materials in structural elements because they are worried about the quality,” she says. “There should be a mechanism to ensure that those materials have a certain quality and strength and can be used in certain building elements. If there’s a guarantee, then people will use those things.”
“People tend to use the easiest method. Time is money,” Udawatta says. “We need to make it easier to reuse materials instead of discarding them.”

Designing for demolition or deconstruction
Demolition waste is another major factor in the environmental impact of the construction industry. When it comes to reducing this waste, forethought is key. If architects and designers consider the future of their buildings from the beginning, there will be less waste in the long term.
“When we are building new buildings, we have to think about the whole life cycle of the building,” Udawatta says.
This includes designing buildings with a flexible layout that could accommodate different uses over time and limiting the use of non-recyclable materials. The Recyclable House from Sanctuary 44 is an example of this kind of construction.
Sustainable demolition or deconstruction would require the same thing as sustainable construction—a market for recycled products.
“If no one is willing to buy materials, there’s no point in demolition companies separating them. It’s a waste of their time,” Udawatta says.
What can small builders do?
Much of the conversation around reducing construction waste centres around large-scale builders and government contractors. But homeowners working on constructing or renovating their own house can use some of the same strategies to reduce the amount of waste their sites generate.
Udawatta recommends spending more time in the design process. This can be costly, but it can save a huge amount of materials from going to waste.
“If you can finalise the design before starting the construction there won’t be as many changes or reworks,” she says. “They will know exactly what they’re going to build instead of building something and then demolishing part of it and redoing it.”
She also suggests sitting down with the entire team that will be working on the site before anything is done. The people Renew spoke to for the case study accompanying this piece agreed.
“There’s a lot you can do if you bear it in mind from day one,” says Eugenie Stockmann, one of the minds behind sustainable urban housing development The Green Swing. “Make it really clear what your expectations are, that minimising waste is an important parameter of the project for you.”
Aside from good communication, using prefab materials and standardised sizes can greatly reduce waste. Some companies will also allow you to return packaging, one of the major waste-producers on building sites.

Looking towards the future
The sources we spoke to agreed that for real change to happen, recycling must become the norm rather than an afterthought. Education and engagement with every level of the industry is needed if things are to improve.
“It won’t happen overnight,” Udawatta says. “When it comes to education, attitudes and behaviour changes, it takes time. There should be marketing strategies, workshops, to educate contractors, consultants and clients about how they can reuse materials.”
There is progress being made. According to the 2018 National Waste Policy, construction and demolition is turning to recycling faster than any other waste stream. From 2006 to 2017, the amount of construction waste that was recycled increased by 34 percent, or 3.4 million tonnes.
As the benefits of reusing and recycling materials becomes more apparent, there’s hope the industry will continue to change. But it needs to be a team effort.
“It can’t be done alone by the waste contractors,” Udawatta says. “There should be support by all the stakeholders involved in the construction industry.”
Tinder for dirt
Systems engineer Cherie Lee often used to joke with her colleagues about creating a “Tinder for dirt”—technology that would promote reuse and recycling of excess building materials by helping construction industry buyers and sellers find each other quickly and easily.
“Contractors at large construction companies don’t always communicate about their individual projects,” Lee says. “I could not believe the scale of the opportunities for internal materials exchange that were being missed daily.”
This year, Lee refocused her consulting business to build a platform to resolve the practical and motivational barriers to efficient reuse and recycling. The result is MatX—Goods and Materials Exchange—a platform that allows construction companies to create and control their own exchanges and sell goods internally, then offer what is not sold to external exchanges full of like-minded constructors. This could potentially save companies money at the same time as diverting perfectly good materials from landfill.
One of MatX’s main selling points is that it enables marketplaces where companies can sell and buy from people they trust, cutting down on the time it takes to vet sellers in a traditional open marketplace.
The underlying goal of MatX is to change norms in the construction industry, to enable companies to “work more collaboratively and use the principle of circular economy to their advantage.” To do that, Lee says industry leaders need to understand firsthand the benefits of reducing waste. “The bottom line is that sustainability must be profitable, not an overhead.”
The site is heading towards a soft launch in September.
Statewide Waste and Resource Recovery Infrastructure Plan: bit.ly/2krLt4u
National Waste Policy 2018: bit.ly/31Vt6pE
Nilupa Udawatta’s paper on barriers to construction waste management: bit.ly/2jXRVzT
Further reading
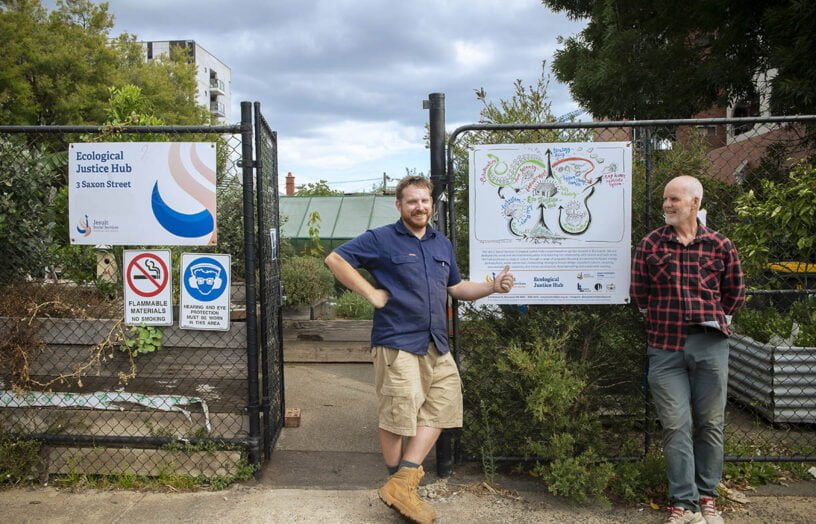
Community eco hub
Nathan Scolaro spends 15 minutes with Stuart Wilson and Michael McGarvie from the Ecological Justice Hub in Brunswick, Melbourne.
Read more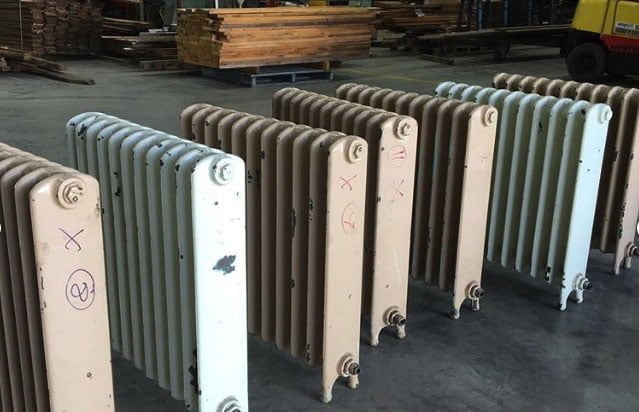
Recycled hydronic heat
Renew’s sustainability researcher Rachel Goldlust gives us a view of and from the Salvage Yard.
Read more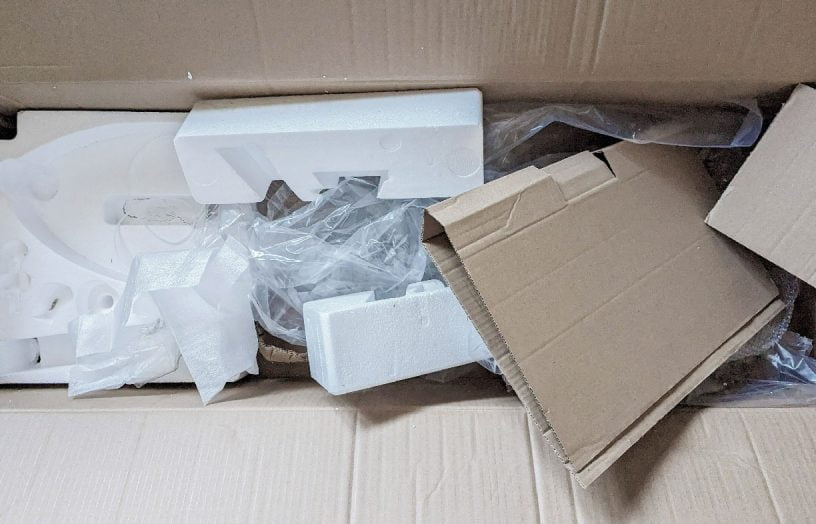
The future of packaging
Packaging comes with just about everything we consume, with far-reaching implications for us and the planet. Jane Hone asks how we can get a handle on it.
Read more