Energy-efficient stained glass
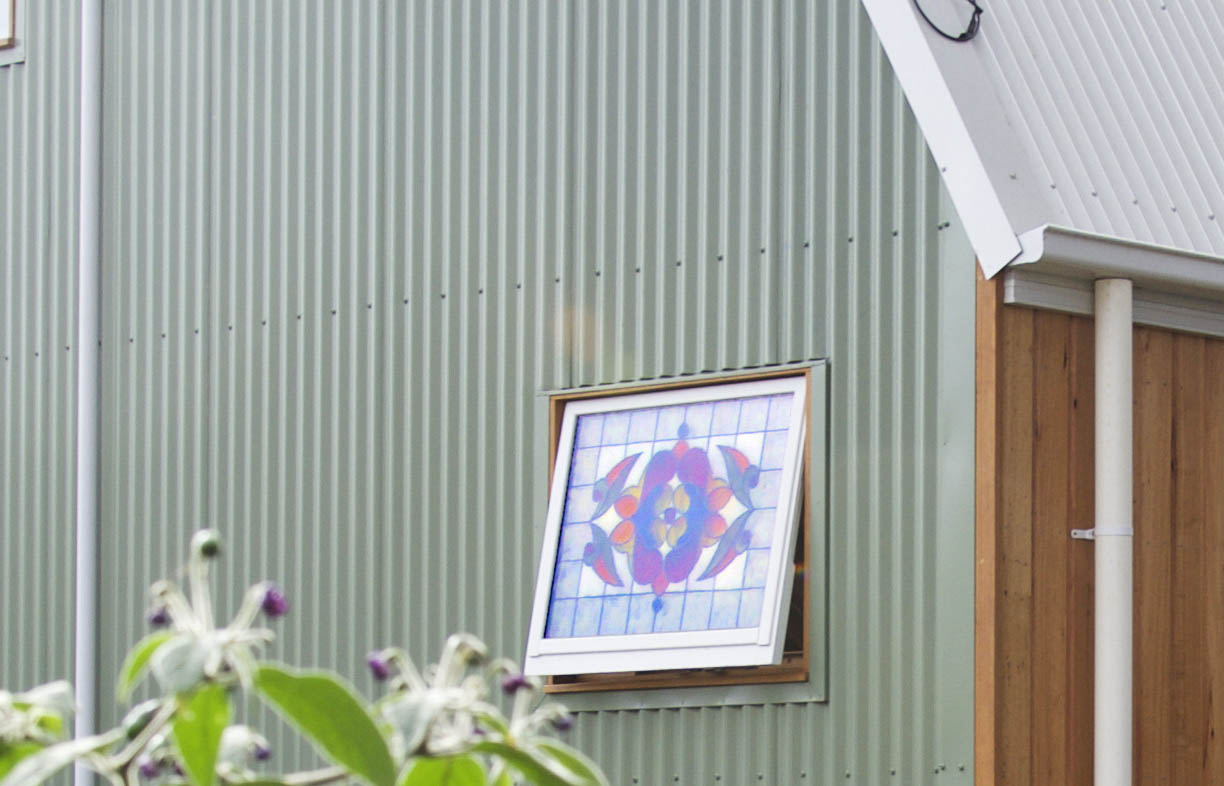
It is possible to reuse old materials in a new energy-efficient build. It just takes a bit of planning and finding tradespeople with the right skills. Vicky Grosser explains.
In 2015 I began the process of building a small house at the back of my property. I was keen to do this in as environmentally sensitive a way as possible, using local skilled people and reclaimed and locally produced material—both to reduce emissions and be respectful to the Wadawurrung Country we were building on. [Ed note: For a full profile of this house, see Sanctuary 43.]
I worked with a draughtsperson friend, Dan Procházka, who’d initially made the suggestion about building the house. Plans were completed, incorporating the carpenter’s ideas such as building the stairs on site from reclaimed wood. Then it was on to the planning process and site sub-division. The build began 18 months later!
In effect this was a bespoke house: we created many aspects as the project was built. In particular, the two stained glass windows I sourced influenced the design. One became the frosted bathroom window on the west side (the only window on that side, to avoid overheating issues with windows on the west). The other is on the south side and can be seen from the street. It’s a lovely welcoming sight, right ahead of you when you walk in the front door.
But how do you go about making very old windows fit into an energy-efficient new build? As an energy efficiency advisor, I wanted the building to perform as well as possible. Here’s what we did.
My part in the process was mainly to source the windows. I was quickly able to source them using Gumtree. The ones I found had been removed from an old cottage as part of a renovation and, at over 80 years old, they were in a vulnerable state and the frames had been damaged when they were removed.
It required excellent carpentry skills, patience and attention to detail for these old windows to be incorporated into a new energy-efficient build. Local carpenter Duff Swanson of Restoration Carpentry took on the upgrade and did a brilliant job. The materials and approach he used could also work for an upgrade of in situ stained glass windows.
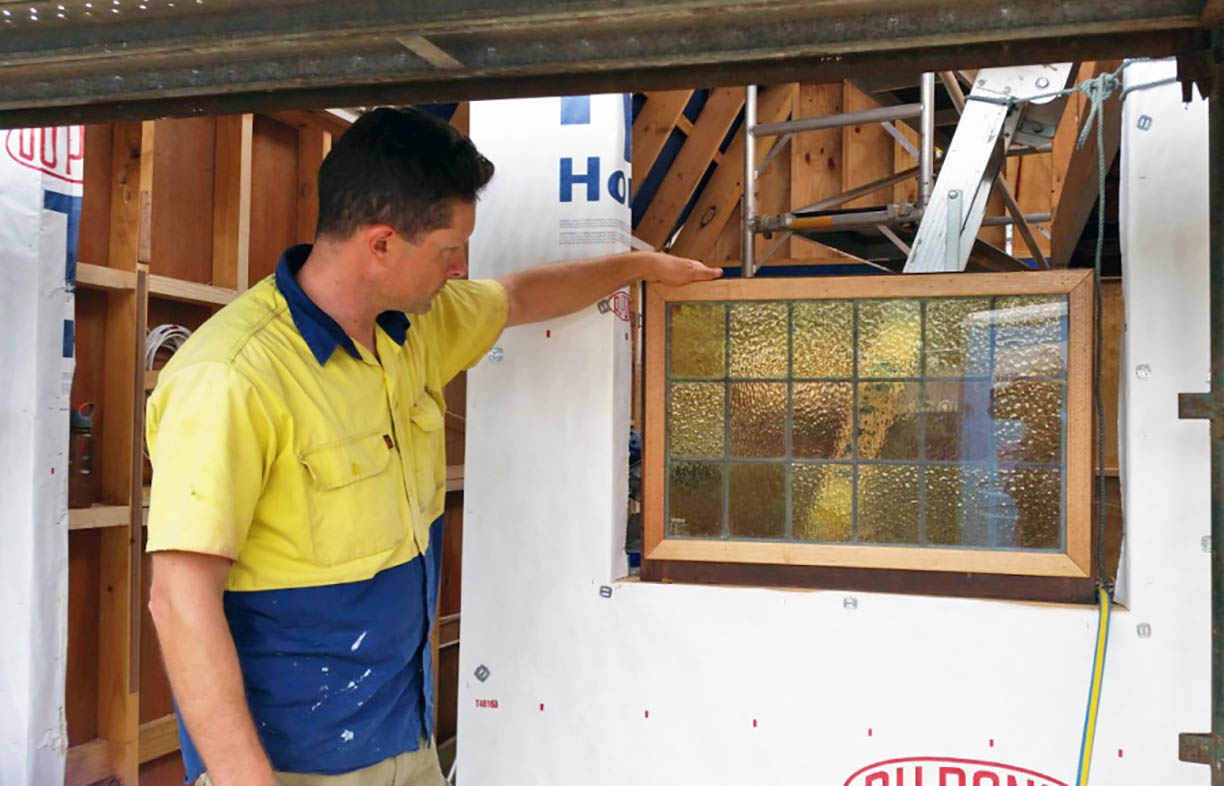
As part of the building process, we required the window upgrades to be approved by a building inspector.
The inspector stipulated that protective glass be fitted to the outside and inside of the windows for safety. For the outside of each window, we used toughened glass. Inside, I negotiated to use acrylic instead of another layer of glass, as it’s lighter, reducing the overall weight of the upgraded window.
The frame needed to include space to install the new glass/acrylic layers with an appropriate 12 mm gap each side for a double glazing effect—or, actually, triple glazing!
To increase the depth of the frame and to fix the old frame, Duff, the carpenter, created a reclaimed blackbutt external frame using timber sourced from local wood reclaiming business Timberzoo. On the inside, he was able to use the original frame, with thin beading fitted to create a gap. We used stain to connect the colour of the old wood (on the inside of the windows) to the blackbutt, which we coated with transparent sealer.
We also added handles, hinges and draught excluder piping (where the window connects with the frame), all supplied by local company Pickering Joinery. The hinges and handles were made to match the six new windows used in the other parts of the house.
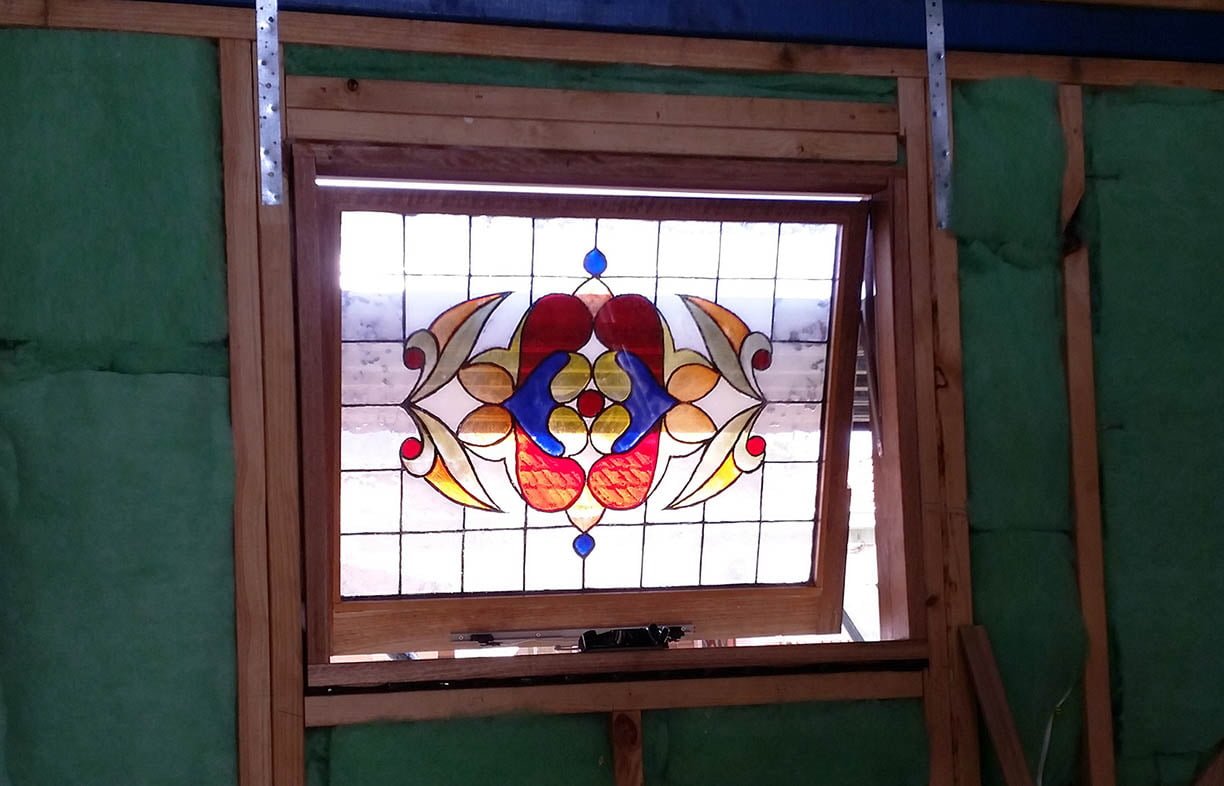
Risks on the upgrade journey
Our biggest concern was breaking the glass in these old windows. Taking time and thinking through each step helped avoid this. Careful measurements were key, of course, to ensure the frame and glass/acrylic panes fitted neatly.
Get skilled help
This approach is not cheaper than buying new windows, but I was happy to put my money into skilled carpentry costs to make these beautiful windows functional. For me, it’s a win-win: I chose to pay people I know to do the job well and use fewer new materials.
This is the type of work which some carpenters are keen to do, outside the construction work they often spend their working days doing.
Building inspector approval
If your build or renovation requires building inspector approval, have a talk early on with the inspector to agree on the process. This ensures appropriate regulations are met for protection and upgrade of such windows.
Design considerations
Consider the window aspect, and external shading to keep out summer sun. With just one small west window, it has been pleasing to notice how well the triple glazing has performed during 40°C afternoon temperatures.
More from Renew 147
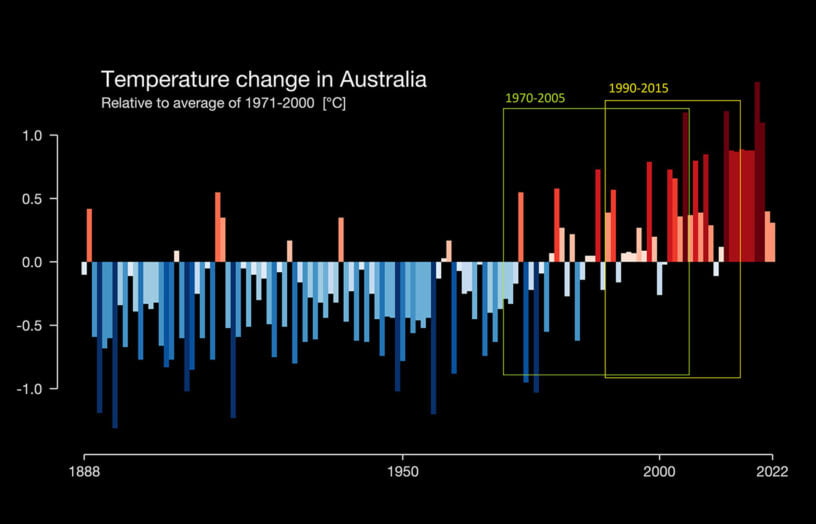
Building for a changing climate
Are we building homes for the future, or for the past? Rob McLeod investigates how climate change is impacting home energy ratings and the way we build our homes.
Read more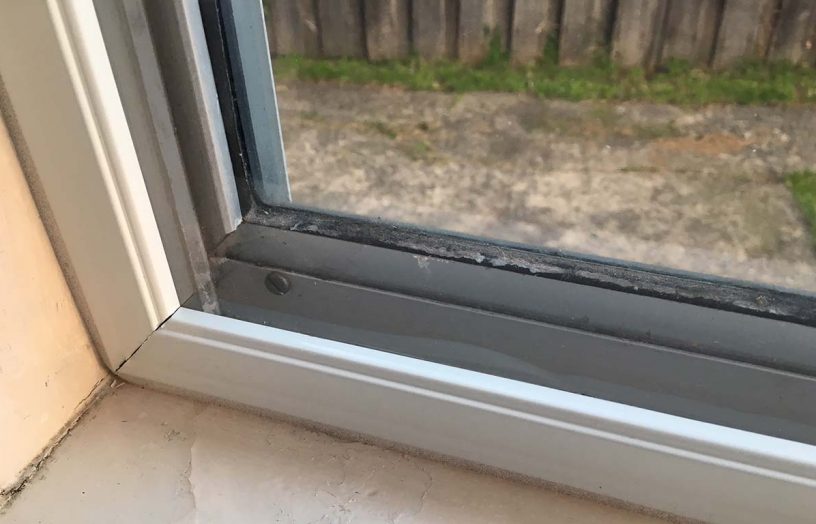
DIY: Insulating aluminium windows
Many Australian houses feature aluminium-framed windows, which perform poorly thermally. But performance can be greatly improved with a simple DIY project. Glenn Newman explains how his friend Lisa Rime came up with an easy system for DIY double glazing.
Read more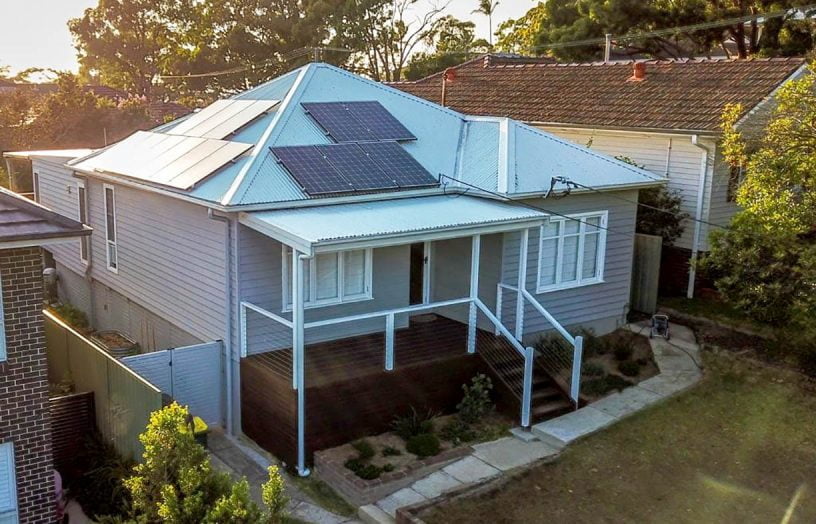
Energy efficiency upgrade: case study
One of six case studies in Renew 147 highlighting how householders have tackled energy efficiency in their homes around Australia.
Read more