A roof over your head: Choosing the right roofing materials

There are many different roofing materials to choose from, but what are the advantages and disadvantages of each, and how sustainable are they? Lance Turner surveys the market.
In ReNew 132 we looked at options available for walls when building a home or extension. But of course there’s more to a home than just the walls—roofing is equally important as it not only protects the rest of the building, but also has to withstand the most intense levels of solar radiation of any part of the home, as well as considerable forces from wind, rain and hail.
The roof must also be able to support added structures such as solar panels and solar hot water systems, satellite dishes, ventilation and air conditioning systems, as well as the weight of people walking on it while installing and maintaining such systems. Plus it’s used to collect rainwater for your home and garden.
There are many different roofing materials available, including corrugated iron and Colorbond steel, concrete, ceramic, metal and composite tiles, slate, shingles and even load-bearing panels such as SIPs (structural insulated panels). Each option has its advantages and disadvantages, each has its own particular look, and each comes in a range of options for that particular material.
Which roofing you go for will depend in part on the materials and the general look of the rest of the home, as well as your personal preference, which may be determined by a number of factors including appearance, the eco-credentials of the material, the range of colours and styles available, the building method (some roofing materials need more structural support than others), the level of maintenance you are willing to give to the roof, the fire resistance level required, and, of course, the location and hence surrounding environment of the home, including heritage or aesthetic requirements of your local council. Let’s look at each material in turn.
Sheet materials
Galvanised iron/Colorbond steel
These materials are made from thin steel sheet (typically less than 1 mm thick) and are coated in either zinc (galvanised iron), an aluminium/zinc/magnesium alloy (Zincalume) or paint over zinc alloy (Colorbond) coating. There’s also a stainless steel-based version of Colorbond for extreme coastal environments.
Steel sheet materials come in a wide range of profiles (the shape, corrugated or otherwise, when viewed end-on), including the common corrugated iron, the mini version (such as Lysaght Mini Orb, which is usually used on walls but can be used as a roofing material), as well as profiles more commonly used for commercial roofing although also suitable for some domestic projects, such as Trimdek, Klip-Lok and numerous others. See www.steelselect.com for information on the sorts of profiles available.
Sheet steel products are all used in a similar manner: they are either screwed (or sometimes nailed) to wood or steel battens, or they are clipped onto concealed brackets which are screwed to the battens. Both methods have the edges of the sheets overlapping to prevent water ingress, but concealed fixing systems eliminate piercing of the sheets associated with screw or nail fastening and provide a more reliable weather seal. Ridges are finished with purpose-made capping and, typically, various designs of gutter complete the eaves’ detailing to provide a neat and clean finish to the roof.
Another technique which uses sheet roofing is the ‘standing seam’ method. Sheet metal ‘trays’ are formed from flat sheets with folded vertical edge seams which interlock and are then crimped down to complete the seam. This allows for very long tray panels to be used (up to 10 metres long) and is suitable for larger roofs and roofs with concave or convex curves. The disadvantage of the system is that once panels are locked together, they are harder to separate compared to sheets that are simply screwed down.
Advantages of sheet steel products are considerable. They are light and relatively easy to handle (although extreme care must be taken during windy days), are easy to fasten and quick to install (for professionals, at least), are very strong and, if installed correctly, will last for decades with minimal maintenance. They are also extremely fire resistant, although heat and sound travels through sheet steel products with ease.
Sheet products have very few disadvantages, but poorly installed sheeting can become a sharp hazard when cleaning gutters if the sheets extend too far into the gutter.
Many sheet steel products contain recycled steel (check datasheets for recycled content and other sustainability features, as it varies between products and manufacturers), and all sheet steel is easily recycled through well-established recycling systems, so there is no reason for these products to end up in landfill at the end of their useful life.
Insulated panels/SIPs
These consist of two sheets, usually coated or painted metal such as Colorbond sheeting, which are bonded to each side of a layer of insulating foam. They are similar to structural insulated panels (SIPs)—indeed SIPs can be used as roofing—but roofing panels such as Ritek’s Custom Roof Panel, Stratco’s Cooldek and Versiclad’s insulated panels range are specifically designed for roofing applications.
They are very strong, lightweight and easily installed, and may provide the first level of both thermal and acoustic insulation to a home. These types of panels are available in thicknesses of 125 mm or more, so insulation levels can be considerable. A quick look around will find domestic-grade SIPs ranging from around R2 to R5 or so.
Maintenance requirements are minimal, much the same as regular sheeting products.
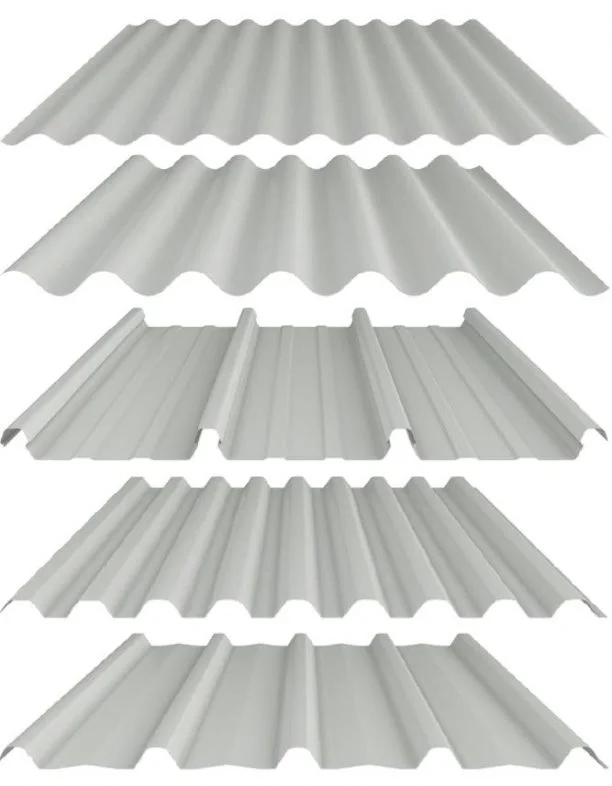
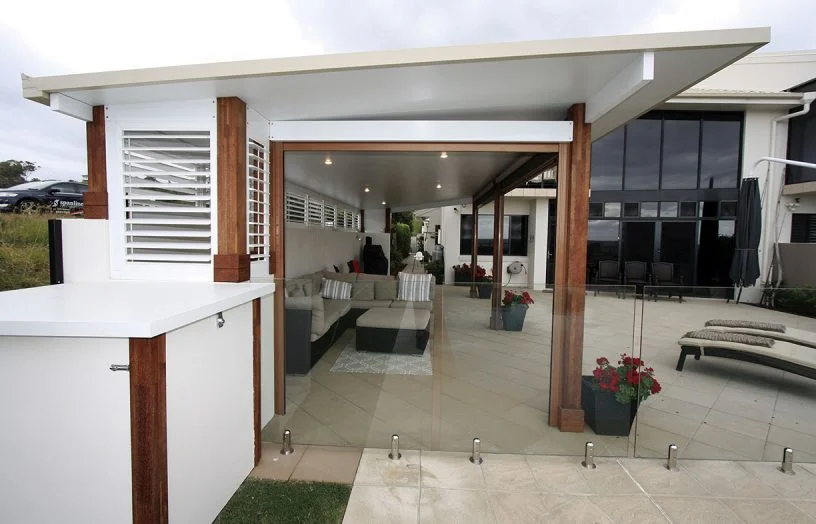
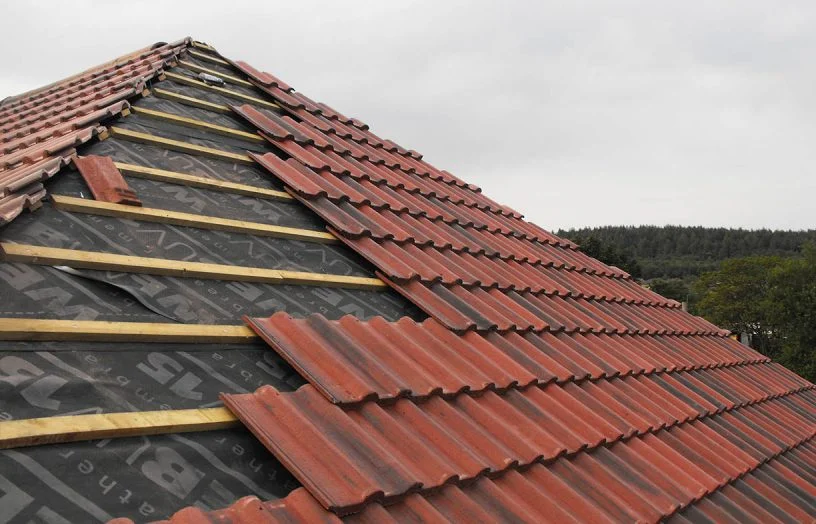
Tiles
Tiles have been a popular option in Australia and the finished result is preferred by many homeowners. All tiles, regardless of the material they are made from, have the advantage that they can be easily replaced if they suffer damage, such as from falling tree limbs, being walked on etc. Unlike with sheet materials, you only need to replace the area that has been damaged, not an entire roof section from cap to gutter. There are quite a few materials used for tiles nowadays, so let’s look at the more common ones.
Concrete tiles
As you might expect, concrete tiles are made from cast/pressed concrete, which is a mixture of cement, sand and pigments. They are available in a wide range of colours and patterns, including traditional styles, flat slate-like tiles, bevelled and textured tiles.
Concrete tiles are relatively fragile as they usually have no internal reinforcing like structural concrete does. They are fairly easily broken if walked upon after being incorrectly fitted (a common problem after rooftop work, such as fitting roof-mounted devices, has been done) or dropped during installation, or if they suffer impacts from falling tree limbs and the like.
Concrete tiles can have a very long lifespan, up to 50 years or more, and if care is taken when a house is deconstructed, concrete tiles can find a second life in another building project. Old tiles can also be recycled by crushing, for use as fill material in new concrete or for other building works.
One disadvantage with concrete tiles is that they are heavy, so while concrete has a relatively low embodied energy per kilogram compared to other roofing materials (see Your Home’s embodied energy page), the high mass per unit area covered compared to sheet and similar products results in a fairly high embodied energy for an overall roof.
Also, this high mass means roofing structures must be able to support the weight of several tonnes of tiles for the life of the building. As tiles are relatively small, roofing battens must also be fairly closely spaced, resulting in more materials use for the roof structure, and more time to install compared to sheet products.
Acoustically, at least two manufacturers stated their tiles will reduce outside noise through the roof by as much as 30 dB, which is considerable, so if noise is an issue then tiles are a good candidate for a roofing material.
Clay tiles
Clay tiles are usually made from terracotta clay fired to around 1100 °C, resulting in a waterproof vitrified tile. They are available in a range of colours and profiles and will have a very long life if cared for. Because they are fired, they can have an embodied energy of around 6.5 MJ/kg (University of Bath, UK, see Wikipedia on embodied energy). While this is lower than steel sheet products, like concrete tiles, clay tiles’ high mass per unit area comes into play, so clay tiles will have a higher embodied energy per total roof area than sheet products.
Being a ceramic, they are quite brittle and easily broken if badly treated, so care must be taken when handling and installing them. Like concrete tiles, broken ceramic tiles can be crushed and used as filler in new concrete or elsewhere as they are an inert material.
Like concrete tiles, clay tiles have a reasonable sound-reducing effect on outside noise, so may be more appropriate in high noise areas such as near main roads and airports. Also like concrete tiles, clay tiles are heavier than sheet roofing materials and so need appropriate supporting structures in the roof, which may add slightly to construction time and costs.
Metal tiles
As you might expect, metal tiles are made from pressed sheet metal and designed to look like more traditional ceramic/concrete tiles. They have the advantages of being lightweight, stronger than masonry tiles and more easily replaced than sheet materials should they be damaged.
Pressed metal tiles are usually either painted, like Colorbond, or have a textured coating that makes them look like a concrete tile. Both coatings can become damaged over time, from falling debris, foot traffic and heavy hail impacts. Metal tiles can also be dented to the point of needing replacement if someone walks in the middle of the tile instead of the top and bottom edges (where the battens are).
One advantage of metal tiles is that a single large tile can take the place of several concrete or ceramic tiles, making for faster installation.
Being predominantly metal (steel or aluminium), these tiles can be recycled through regular metal recycling channels.
Note that there are very few suppliers of metal tiles in Australia, but a hybrid style metal tile/sheet is available from at least two suppliers (Metile and Austech Roof) which consists of Colorbond sheets pressed to look like strips of tiles. The result is a roof that is easy to lay like sheet steel products while producing the look of tiles.
Slate tiles
Slate gives a nice look to a roof, but slate is relatively fragile and heavy and requires a skilled roofer with slate installation experience to install it. If considering slate, you should find a slate supplier/installer with long-term experience.
While embodied energy of slate production is quite low, nearly all roofing slate in Australia is imported, adding to the energy debt of the material. Further, slate quarries can cause considerable damage to their local environment. However, slate has a very long lifespan if installed and cared for correctly.
Composite tiles
These are made from reinforced plastic composites, much like recycled plastic decking that has become popular in recent years, although composite tiles use virgin resins (not recycled) for longevity.
One example, Monier’s Elemental series, comes in four sizes—the Slate (326 x 300 mm), the Shingle (450 x 350 mm) the Square (750 x 750 mm) and the Ultra Panel (1500 x 750 mm)—with a slate or stone finish which gives a slate tile/shingle look to the finished roof.
Some composite tiles are made to look exactly like traditional slate, but are lighter and easier to use. An example of these is the SVK slates from Premier Slate in NSW, made from fibre-cement sheet. Another slate-like tile range is Tapco’s Inspire slates, made from recyclable plastic and dolomitic limestone, and available in Australia from Bellstone. Yet another option is Authentic Roof slates from Authentic Roof Australia.
Composite tiles are much lighter than clay, concrete or slate tiles per unit of area (Authentic Roof slates, for example, are a quarter of the weight of actual slate) and much stronger, and are resistant to UV and hail. Monier provides a 30-year warranty on their Elemental range, while Tractile also provides a 30-year warranty and a stated lifespan of up to 50 years. Authentic Roof slates come with a 50 year warranty.
While the embodied energy of composite tiles is relatively low compared to other materials, they are less reusable/recyclable due to being a mix of plastic and reinforcing fibre. Currently there are no readily available composite material recycling systems in Australia, although it is worth contacting the respective manufacturers of these systems regarding future recycling plans.
Asphalt shingles
These are common in the USA but not so much in Australia. They are made of thin sheets of felt material impregnated with asphalt, then coated in another layer of asphalt on both sides. Mineral stabilisers are added to increase fire resistance and durability, and the top surface is coated with coloured crushed rock to produce the final finish.
Asphalt shingles are not a structural roofing material in themselves, but more a final finishing material, being laid over sheets of marine-grade ply that provides roof rigidity and support. There is usually another layer of asphalt-impregnated felt or similar material laid down over the ply before the shingles, to improve weather resistance of the final roof, so their installation is more complex than most other roofing systems.
However, because the shingles are light, thin and flexible, and roof capping is done using the same shingles folded over ridges, asphalt shingles are easy to work with, making them suitable for DIY use—although their installation can be a little time-consuming.
If installed according to the supplier’s guidelines, lifespan can be 50 years or more, and they come with warranties of up to 40 years. There is debate as to the safety of using rainwater collected from asphalt shingle roofs. There seems to be no definitive resolution of this debate, although a 2010 report from the Texas Water Development Board showed that asphalt roofs are similar to other roofs such as steel and tiles, especially when used with a first flush diverter (as all roofs should be).
Wood shingles and shakes
Timber shingles and shakes (a thicker shingle, sometimes with a coarse textured surface) are arguably the most sustainable roofing material as they are completely renewable and biodegradable, provided they come from suitably sustainable sources.
They are simply pieces of timber cut into tile-sized boards of a fixed height but variable widths, usually between 10 mm and 14 mm thick at the butt (the thick end), or up to 25 mm for shakes. They are simply nailed into place and then given a coating of wood oil or other preservative if desired, although some can be left au naturel.
Like asphalt shingles, wood shingles are usually fixed over a plywood substrate, which provides the majority of roof strength, as well as a continuous surface to nail into, so shingles can vary in size without complex batten systems.
While most other tiles are made in a factory, timber shingles can be made from any suitable timber and even cut on site with the right equipment. However, they are also available pre-made and at least one supplier, Cedar Sales, can provide western red cedar shingles with FSC and GreenTag certification.
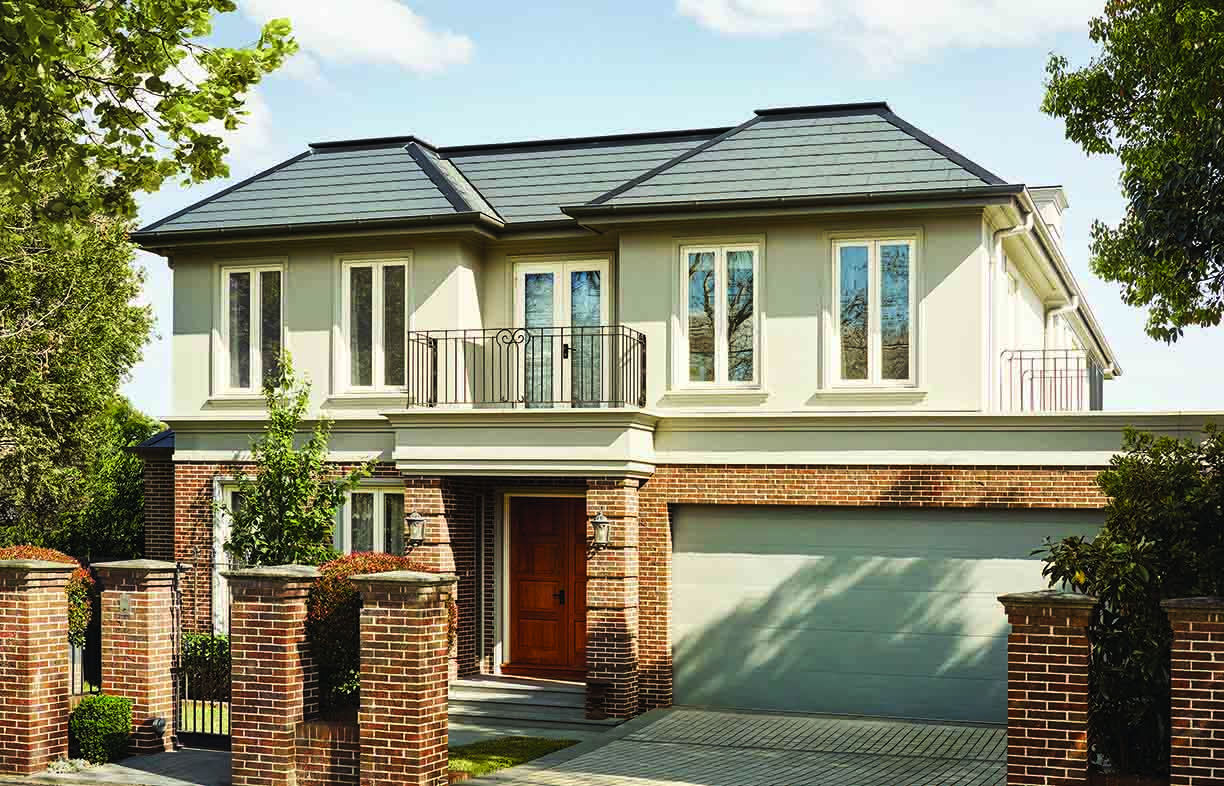
Transparent/translucent sheeting
Often used for verandahs or garages, transparent or translucent materials transmit light into an area and fall into three common types: polycarbonate, PVC and fibreglass.
They are all used just like regular sheet products, and indeed have the same profiles, so that one or more sheets of steel roofing can simply be replaced with transparent sheets.
Because of their lower strength compared to steel sheets, they usually require load-spreading washers specifically designed for their profile to prevent screws pulling through the sheet during high winds.
Polycarbonate sheets are the most common form of light-transmitting sheets used for domestic roofing. They are available in a range of profiles and a wide range of tint colours and light/heat transmission ratings, from completely transparent through to almost opaque. Polycarbonate roofing can be expected to last at least 15 years in most situations, and often a lot longer.
A variation on polycarbonate sheeting is cellular sheeting, which consists of two or more parallel sheets separated by small walls to form many parallel tubes. This material is generally flat rather than profiled, and ranges from 3 mm thick to 40 mm or more for commercial grades. It is commonly used in greenhouses and commercial facades but has also found use in domestic light walls (in place of windows but more robust and private, for example, www.bit.ly/2fth9B0) and feature walls. Typical materials include Suntuf Sunlite and the Ampelite range of domestic- and commercial-grade sheeting.
Cellular polycarbonate sheeting does offer some insulation capability. The air trapped in the cells of the material forms an insulating blanket similar to double glazing and some of these panels may offer quite a high thermal insulation performance, helping to reduce heat loss from interiors—one reason they are used in some commercial greenhouses. One manufacturer, for instance, claims that their 10 mm Suntuf Sunlite Twin Wall Polycarbonate sheeting has a U-value of 2.9, which compares well with a U-value of 2.7 for an air-filled double-glazed aluminium-framed window.
PVC is similar to polycarbonate, just cheaper and more environmentally damaging to produce. It is also not generally recommended for full sun exposure and so isn’t used extensively.
Fibreglass sheeting comes in a range of profiles, colours and light and heat transmission levels, much like polycarbonate sheeting. However, having glass fibre reinforcement can make it stronger than other light-transmitting sheeting products. Many readers will have seen degraded fibreglass sheeting and consider it to have too short a lifespan, but products such as Ampelite’s Wonderglass GC, which has a chemically bonded UV resistant coating that virtually eliminates surface degradation and loss of light transmission, have addressed this issue.
The main environmental drawback with virtually all light-transmitting roofing sheets is the lack of recyclability at end of life. Very little recycling of polycarbonate and PVC is done in Australia; roofing sheets are usually too degraded by weather and UV damage to be recyclable in regular recycling streams, even if recycling schemes are available. Fibreglass is even more difficult to recycle as it is a composite material consisting of polyester resin and glass fibres.
Untinted transparent roofing sheets also transmit a great deal of the infrared radiant energy falling on them, so they have almost no insulation capability. Tinted roofing sheets, which come in a number of colours and light transmittence levels, can be more effective at reflecting heat. Some materials, such as Suntuf SolarSmart, are designed to pass a good percentage of visible light while reflecting up to 85% of infrared, depending on the tint.
As these materials are usually used outdoors, some heat transmission is generally not a problem, but when used on garages or hybrid living spaces, such as sheds converted to living spaces, the ingress of high levels of heat can be a problem, so the stronger infrared reflecting materials should be used. In summer, even a small amount of infrared entering through the roof can make a room unlivable. This can be mitigated by the use of an external blind or shutter, but in general, transparent roofing sheets are not suitable for use in enclosed living spaces unless your home is located in a very cool climate.
What’s the best roof design?
There is no simple answer as it depends on a number of factors, including the design of the rest of the house, the house location and orientation, climate, and the need to accommodate other roof-mounted equipment such as solar arrays.
The roof design will influence the range of suitable roofing materials. For example, near-flat roofs must usually use sheet metal or SIPs-type materials as tiles will suffer from water ingress, due to rain being blown back under the tile edges in high winds. It is possible to seal behind tiles for such situations, but flat roofs generally look better with sheet products—tiles just don’t suit a flat roof.
Roof angle should be carefully considered. Flat roofs, while simple, have some disadvantages. For a start, they often don’t allow much space for good levels of insulation, although this can be solved with better design or using SIPs. However, in areas that experience high temperatures, a flat roof is rarely the best option. Flat roofs also usually require solar panels or solar water heaters to be mounted on tilting frames, which can be unattractive and add to the cost of installation, as well as substantially increasing wind loading on the roof.
Another issue with flat roofs, at least in high rainfall areas, is whether they are able to shed water rapidly enough. Steeper roofs shed rain more easily, and this results in other debris such as accumulated dirt, leaves etc being removed more readily than with a flatter roof.
The common roof styles found in most Australian suburbs involve roof angles of between 15 and 30 degrees, although it varies. In years gone by, the standard roof pitch (known as a quarter pitch) was 22.5°, but nowadays anything goes, depending on the requirements of the homeowner, builder and local council (some councils have a minimum requirement, such as 25°).
Roof pitch can also have an effect on the cost of the overall build, with higher pitched roofs seeing a greater wind loading and so needing to be structurally stronger, as well as having a larger surface area and so needing more roofing materials. So, while that high-pitched roof might look nice, consider what it is doing to the building budget. Of course, if you design the house such that the steep roof can accommodate a living space instead of adding a conventional second storey, the equation changes and the higher pitch may actually reduce the build cost.
Thermal properties
With the exception of SIPs, the insulating abilities of most roof materials are minimal compared to the overall insulation requirements for a thermally stable home, so the slightly higher insulation abilities of one material over another should not be a deciding factor in roof material selection. The insulation inside the roof cavity, such as reflective foil sarking and bulk insulation, has a much higher R-value than most roofing materials.
Sheet steel and metal tiles have almost no insulating properties of their own. The exception to this is products that are very light coloured, or have proprietary heat-reflecting coatings, such as Colorbond Thermatech, which can reduce the incoming radiant energy into a roof cavity.
While concrete, clay and composite tiles have a greater insulating ability than metal products, this will still be low. Slate has a high thermal conductivity and therefore low insulative value. For example, 25 mm slate is rated at a very low R0.1 (US units) or R0.018 in SI units (used in Australia).
Concrete, clay and slate tiles have a high thermal mass, which means they store heat quite well. This is generally a disadvantage in warm months when that results in a hot blanket of material on top of a house which is desperately trying to cool down! The low mass of roof sheeting products means that although they may absorb heat quickly, they also radiate it quickly, unlike concrete or ceramic tiles. Composite tiles can be expected to perform better thermally than concrete or clay tiles, and without the high thermal mass. Because of the plywood substrate, and the insulating ability of the shingles, asphalt and wood shingle roofs have a small but measurable amount of insulation ability.
Keeping the house cool
Insulation
As mentioned above, roof design must allow for adequate insulation to be installed to enable the house to perform well thermally. Most roofs with an accessible roof cavity will contain bulk insulation on the ceiling as well as foil sarking under the roofing material.
Ventilation
Another heat reduction strategy for cavity roofs is good ventilation, which can be in the form of passive or forced ventilation. In passive ventilation, vents are positioned at opposite sides of the roof to allow for cross-ventilation from breezes. A common but fairly ineffective form of forced ventilation is the rotary ventilator, which is spun by the wind and uses either a set of fan blades or the venturi effect to try to extract hot air from the roof cavity. However, hot days are often still days, with insufficient wind strength to extract enough hot air from the roof cavity to make any difference.
A better option is a suitably sized solar ventilator, which uses a solar panel coupled to a DC fan to extract hot air. To be effective, any ventilator must be able to extract the entire volume of the roof cavity every 10 minutes or so, and even faster on very hot days, so you need an appropriately sized ventilator, or several smaller ones. If a home already has a solar array fitted to the roof, it is simpler and more cost-effective to use a mains-powered ventilator, as it will draw its power requirements from the solar array anyway (barring any large loads like air conditioning, which might absorb all available solar power).
Ventilation isn’t used just for temperature control, it also reduces moisture buildup and the associated problems, such as mould growth and rot occurring in structural timber. However, how much ventilation is required, and when it should be active, depends on the design of the home, its level of air tightness, and the local climate. For example, a well-sealed home will benefit from a well-sealed roof cavity in winter as it will help contain warm air inside the building envelope and reduce thermal losses from the living spaces, especially on cold, sunny days.
All of the ins and outs of roof ventilation are too complex to go into here and should be addressed when the home is designed. For homes being re-roofed, then an inspection should be made to determine if moisture has been a problem, and appropriate levels of ventilation included to address any issues.
Roof colour
While insulation in the roof cavity will greatly reduce heat ingress into the living spaces, it makes sense to reduce heat ingress into the cavity itself as much as possible. In general, light-coloured roofs will reflect more heat than dark colours, although many councils have limits on how light a roof can be—white roofs are often frowned upon or simply not allowed.
Some materials, such as Colorbond sheets, have infrared reflective coatings that can help reduce the roof cavity temperature by reflecting more infrared than regular paint or tiles of a similar shade, despite still appearing quite dark. While there is no magical substitute for a lighter-coloured roof, such coatings can reduce the heat load of a home somewhat.
Note that there are thermally reflective paints that can be used to reduce heat ingress on dark roofs. A typical example is Thermoshield which uses hollow ceramic beads in a white binder to produce a paint that reflects a higher proportion of the solar radiation that falls on its surface. These types of paints mean that you end up with a white roof, so check with your council as mentioned above.
Shading
Of course, shading will also greatly reduce the level of incoming heat, but if you plan to fit solar panels to your roof, then shading is not an option. However, the panels themselves can provide a degree of heat reduction. While they will heat up and reradiate some of that heat from their rear surface towards the roof, the amount of heat reradiated will be considerably less than from direct radiant sun on that portion of the roof. On a sloping roof, with a reasonable gap between the panels and roof (at least 50 mm), convective airflow between the panels and roof can occur, helping to reduce temperatures for both panels and roofing.
In summary
We hope this brief introduction gets you started with thinking about the materials and design for your roof—there can be a lot to consider to ensure you get the roof that performs to your requirements.
If you are looking to re-roof your home and don’t yet have solar panels for electricity generation, then you should seriously consider building-integrated photovoltaics (BIPV). These are solar panels that take the place of some, or even all of the roofing material, providing an integrated look to the solar array. There are now at least four suppliers of BIPV systems in Australia:
- Stratco’s Solatile (available in SA and Qld).
- Monier’s SolarTILES, which integrate with Monier’s range of flat profiled concrete roof tiles, the Horizon, Madison, Georgian and Cambridge.
- Star 8 Solar supply solar roof tiles that are compatible with the majority of Australian tiled roofs.
- Tractile’s Eclipse solar roof tile, which integrates with their Eclipse composite and Eclipse Thermo roof tiles to form a complete roof system that not only provides solar electricity, but solar hot water as well. Tractile also has a tile, the Horizon tile, with combined PV and hot water collector that integrates into existing roofs fitted with Boral concrete roof tiles.
Tesla has been expanding operations by moving into the energy storage and generation markets, and recently released a range of four different solar tile products designed for complete roof integration. They are made of impact-resistant glass with a solar PV layer and a special optical layer so that they only look like PV panels from above, not from the ground.
The really interesting aspect of these tiles is the price. Tesla CEO Elon Musk has stated that the price of a Tesla solar roof will be the same or cheaper than an equivalent non-solar tiled roof (so, for example, a solar slate roof versus a regular slate roof). This has been made possible by streamlining the supply chain compared to regular roofing materials, as well as the tiles being lighter than masonry tiles. However, no pricing information has been released, so actual pricing is unknown—we expect that it will only compare directly on price with the most expensive roof types, such as slate tiles. The tile range is expected to be released some time in 2017.
While you might think that combining both the roofing material and the solar panels would reduce costs compared to a regular roof with panels added on top, this generally isn’t the case yet. However, total costs vary for each method of PV installation, the advantages of BIPV such as the more integrated and neater installation, elimination of roof penetrations, and reduced roof debris buildup and hence easier cleaning can more than make up for a slightly higher cost over a separate roof plus PV installation.
Just as conventional solar panels have reduced massively in price with the increasing uptake of the technology, BIPV systems will become more cost effective than regular systems as their popularity grows.
BIPV panel efficiencies vary and the tile systems generally have lower efficiencies than regular PV panels as their construction requires extra area for the roof integration component. For example, Stratco’s Solatile measures 1662 x 995 x 5.5 mm with its integrated 205 W polycrystalline panel, giving it an efficiency of around 12.4%—somewhat less than most polycrystalline panels.
For the 33 W Monier SolarTILE, which is around 0.25 m2 once fitted, the efficiency is around 13.2%, so approaches conventional polycrystalline solar systems.
However, the smaller panel sizes of some BIPV systems can allow for more flexible panel placement compared to the much larger panels found in on-roof PV systems.
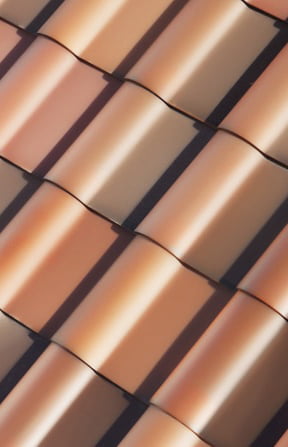

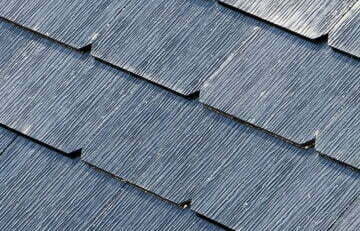

The vast majority of roofs on Australian homes are conventional—Colorbond/galvanised, tiles, slate or shingles. However, there is another type of roof that can perform better thermally than any conventional materials—a green roof.
A green roof is simply a roof designed to grow plants. A layer of growing medium—soil or lightweight aggregate—is laid on a suitably prepared and designed roof structure, which may include waterproofing, root barrier and drainage system. The roof is planted out with appropriate plant species.
The insulating and thermal mass properties of a green roof can help stabilise internal room temperatures and reduce sound ingress while helping the house to blend into the surrounding landscape—ideal for homes in wilderness areas.
Other advantages include the reduction of the urban heat island effect, where large surfaces of concrete and bitumen absorb heat rather than reflecting it, reduced stormwater runoff, improved air quality and creation of habitat for wildlife.
Green roofs fall into two main categories: extensive and intensive.
Extensive roofs are those with growing medium thickness under 200 mm. They have a relatively low roof loading of up to 120 kg/m2 and use low mass plants like sedum or other low growing succulents, ground covers and mosses, grasses and small ferns. Extensive green roofs are normally designed to require minimal care and are usually only accessed for maintenance, so most extensive roofs will only grow simple plants that require little effort.
Extensive roofs can be laid on lightweight roofs using structures not much different from those suited to Colorbond roofs, for instance, and in some cases, subject to structural limitations, can be laid on top of existing lightweight roofs.
Intensive green roofs use a growing medium depth over 200 mm with much higher roof loads of up to 700 kg/m2 or more. They can include high mass plants like large shrubs and small trees, and are designed to be used and maintained regularly, so they can even be used for growing herbs and vegies.
As you might expect, only certain structures are suitable for green roofs due to the high mass on the roof. Buildings made of concrete and stone or other materials with high compressive strengths are required—heavy steel or timber structures can be suitable, but the engineering must be carefully calculated.
Green roofs can be either flat or near-flat (the usual format for an intensive roof) or sloping. A sloping roof increases the water run-off from the roof during rain, so less water is retained and waterproofing is less critical. In an intensive roof, waterproofing must not only last the life of the building, it must also be able to withstand plant root penetration from more aggressive plants such as small trees.
This leads us to the costs of green roofs. A simple extensive roof may cost up to a few hundred dollars per square metre, not including any building permits and fees, roof strengthening or moving of roof infrastructure. An intensive roof can easily cost into the thousands of dollars per square metre due to the high structural strength and levels of waterproofing and root barrier required—and the cost of the much thicker layer of growing medium and more expensive plants than extensive roofs normally have. Actual cost will depend on many factors.
For most domestic situations, an extensive roof is probably the best option, but if your garden space is otherwise limited, then an intensive green roof can double as an outdoor living space, potentially offsetting the higher cost of this sort of roof.
Further reading:
A useful guide on planning a green roof is the Growing Green Guide.
Your Home green roof page
Green Roofs Australasia
Wikipedia green roof page
Roofing Tile Association of Australia
Metal Roofing and Cladding Association of Australia
Master Builders Australia
Note that individual states may also have their own roofing associations.
Related articles
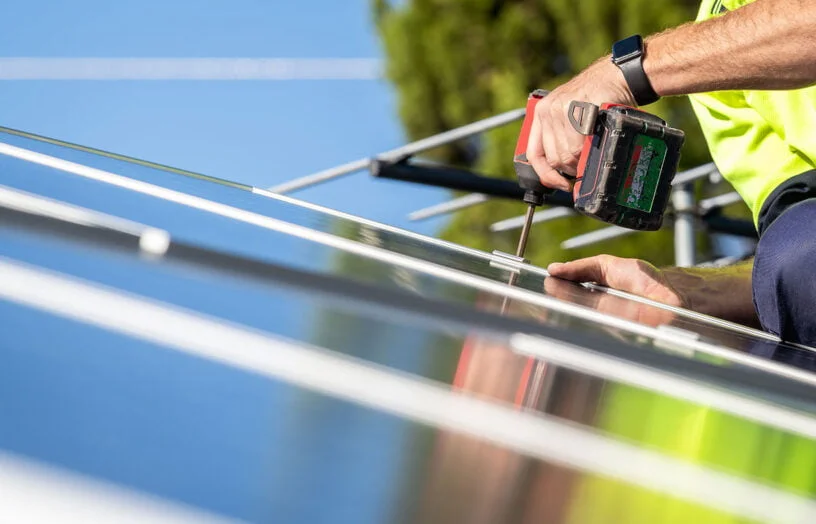
Tradies and the transition
Do we need as many tradies for electrification as many think? Not if we are innovative, writes Alan Pears.
Read more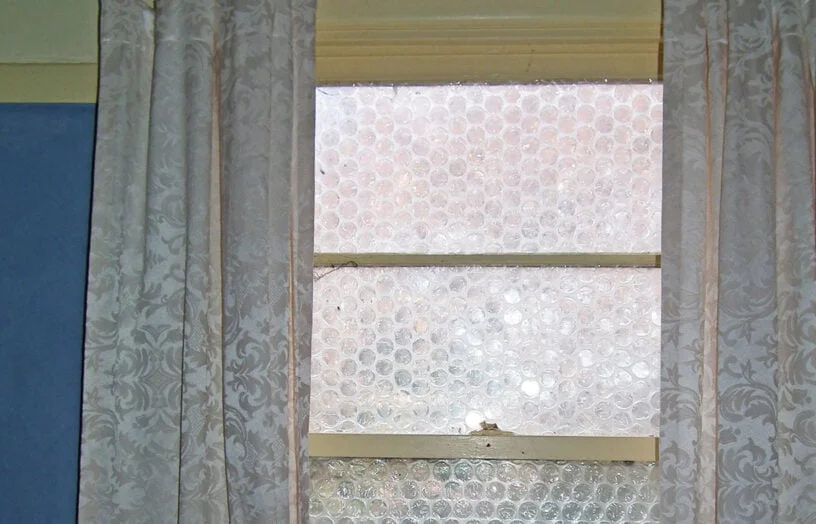
Double glazing on the (very) cheap
Do we need as many tradies for electrification as many think? Not if we are innovative, writes Alan Pears.
Read more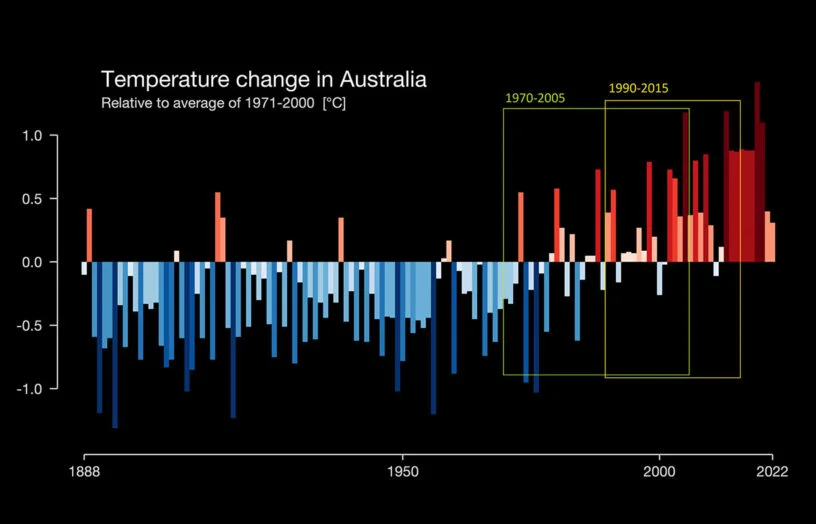
Building for a changing climate
Are we building homes for the future, or for the past? Rob McLeod investigates how climate change is impacting home energy ratings and the way we build our homes.
Read more